PHILIPS VR2022S VIDEO 2000 Reversable video cassette:
1. Video-Wendekassette in Form eines im wesentlichen quaderf·ormigen K·orpers mit zwei darin drehbar gelagerten Wickelspulen f·ur das Magnetband und einer an einer schmalen L·angsfl·ache vorgesehenen ·Offnung mit teilweise zur·uckgesetzter Geh·ausewand zur freiliegenden Magnetbandf·uhrung, wobei die Kassette vorzugsweise aus zwei verriegelbaren im wesentlichen geschlossenen Halbteilen besteht, die zur Ver·anderung des Wickelspulenabstandes sowie zur Vergr·osserung der freiliegenden Magnetbandl·ange verschiebbar gelagert sind, d a d u r c h g e k e n n z e i c h n e t , dass die Verbindung der verschiebbaren Kassetten
-Halbteile (7,8) durch zwei flache F·uhrungsteile (13, 14) erfolgt, die in parallel angeordneten F·uhrungsnuten (19, 20), die sich in den beiden ·ausseren schmalen L·angsfl·achen (15, 16) der Geh·ausehalbteile befinden, eingelegt sind, und die Verriegelung der beiden Halbteile durch zwei seitenversetzt den F·uhrungsteilen zugeordnete Sperrhaken (17, 18) erfolgt.
2. Video-Wendekassette nach Anspruch 1, d a d u r c h g e k e n n z e i c h n e t , dass die F·uhrungsteile (13, 14) aus schmalen bandartigen Metallstreifen bestehen.
3. Video-Wendekassette nach den Anspr·uchen 1 und 2, d a d u r c h g e k e n n z e i c h n e t , dass die F·uhrungsteile aus antimagnetischem Federstahlband bestehen.
4. Video-Wendekassette nach Anspruch 1, d a d u r c h g e k e n n z e i c h n e t , dass der aus Kunststoff einst·uckig gefertigte Sperrhaken (17, 18) aus einem Hakenteil (22), einem Lagerauge (23) und einem Verbindungssteg (24) besteht, wobei der Verbindungssteg eine Schr·agfl·ache (27) aufweist.
5. Video-Wendekassette nach den Anspr·uchen 1 und 4, d a d u r c h g e k e n n z e i c h n e t , dass der Sperrhaken mittels einer Druckfeder (25) in einer die beiden Kassetten-Geh·ausehalbteile verriegelnden Lage gehalten wird.
6. Video-Wendekassette nach einem der Anspr·uche 1 bis 5, d a d u r c h g e k e n n z e i c h n e t dass die Verriegelung der beiden Kassetten-Halbteile durch Eintauchen wenigstens eines Stiftes (9, 10) in die Kassette aufgehoben wird, wobei der Stift auf die Schr·agfl·ache (27) des Sperrhaken-Verbindungssteges (24) trifft und den Haken aus einem Sperrzahn (26) hebt.
7. Video-Wendekassette nach Anspruch 6, d a d u r c h g e k e n n z e i c h n e t , dass f·ur jeden Sperrhaken ein Stift zur Entriegelung in die Kassette eintaucht. EMI11.1
Es sind Magnetbandkassetten bekannt, bei denen die Bandwickelspulen mit einem bestimmten Abstand nebeneinander in einem Kassettengeh·ause angeordnet und die Wickelspulen von aussen ·uber ger·ateseitig angeordnete Antriebsmittel antreibbar sind. Weiterhin sind auch Kassetten bekannt, die eine Ver·anderung des Abstandes der Band wickelspulen erm·oglichen. Derartige Kassetten finden insbesondere bei Videoger·aten Anwendung. Bei Ger·aten dieser Art werden von Seiten des Benutzers, je nach Verwendungszweck, differenzierte Anforderungen gestellt.
So wird z. B. zwischen netzabh·angigen Heimger·aten und netzunabh·angigen, also batteriebetriebenen, tragbaren Ger·aten unterschieden. Hierbei spielt insbesondere das Gewicht und die Gr·osse der unterschiedlichen Ger·ate eine erhebliche Rolle. So ist die Gr·osse des Ger·ates in erheblicher Weise von der Gr·osse der Kassette abh·angig.
Bei einem tragbaren Videoger·at, das beispielsweise die Bildaufzeichnung mit Hilfe einer Videokamera erm·oglichen soll, ist eine lange Aufnahmedauer, wie sie bei einem Heimger·at gew·unscht ist, nicht erforderlich. Dagegen spielen jedoch das Gewicht und die Gr·osse bei einem tragbaren Videoger·at eine erhebliche Rolle.
Aus den unterschiedlichen Anforderungen eines Benutzers an ein Video-Heimger·at einerseits und ein tragbares batteriebetriebenes Videoger·at andererseits ergeben sich zwangsl·aufig abweichende Kassettengr·ossen mit unterschiedlicher Spieldauer. Der naheliegende Wunsch, dass die kleinere, f·ur tragbare Videoger·ate geeignete Kassette, auch auf einem f·ur gr·ossere Kassetten eingerichtetem Heimger·at abgespielt werden soll, ist schwerlich zu realisieren.
Es ist zwar bereits eine Kassettenkonstruktion bekanntgeworden, bei der auch kleinere Kassetten in einem Video-Heimger·at f·ur gr·ossere standardisierte Kassetten abgespielt werden k·onnen, die daf·ur erforderliche Konstruktion ist jedoch recht kompliziert und damit teuer.
So werden gem·ass diesem Stand der Technik Zahnrad·ubersetzungen erforderlich, mit deren Hilfe der Bandwickelabstand ausgeglichen wird.
Ein weiteres Ausf·uhrungsbeispiel zur Anpassung einer kleineren Kassette in ein Heimger·at, das nur f·ur eine gr·ossere Kassette geeignet ist, sieht vor, dass die Wickel spulen in einer besonderen Lagereinrichtung schwenkbar gelagert sind. So k·onnen die Wickel spulen mit einem kleineren Abstand in ein kleineres Kassettengeh·ause und nach Verschwenken in ein gr·osseres Kassettengeh·ause eingesetzt werden. Eine Ausf·uhrung dieser Art ist ebenfalls aufwendig und erfordert vom Benutzer ein besonderes technisches Geschick.
Eine diese Nachteile teilweise vermeidbares Ausf·uhrungsbeispiel einer Kassette zur Ver·anderung des Wickelspulenabstandes sieht vor, die Wickel spulen in getrennten, zueinander verschiebbaren Geh·ausehalbteilen unterzubringen. Die beiden Geh·ausehalbteile werden hierbei durch einen als Hohlzylinder ausgebildeten F·uhrungsabschnitt in einer festen Bewegungsbahn gef·uhrt.
Nachteilig ist hierbei, dass die F·uhrung der beiden Geh·ausehalbteile keinerlei Anpassung der auseinander gezogenen Kassetten-Geh·ausehalbteile an die Lage des im Heimger·at ver·anderten Wickelspulenantriebs erm·oglicht.
Der Erfindung liegt die Aufgabe zugrunde, eine relativ kleine Video-Wendekassette f·ur tragbare Videoger·at zu schaffen, die mit geringem technischen Aufwand auch in einem f·ur gr·ossere standardisierte Kassetten vorgesehenem Video-Heimger·at abgespielt werden kann, wobei sich der Wickelspulenabstand in der Kassette dem Spulenantrieb im Heimger·at zwangsl·aufig anpasst.
Die L·osung dieser Aufgabe erfolgt erfindungsgem·ass durch die im kennzeichnenden Teil des Anspruchs 1 angegebenen Massnahmen.
Vorteilhafte Weiterbildungen ergeben sich aus den Unteranspr·uchen.
Die Erfindung wird nachfolgend unter Bezugnahme auf die Zeichnungsfiguren beispielsweise erl·autert. Es zeigt: Fig. 1 eine perspektivisch dargestellte Video-Wendekassette mit abgenom mener Abdeckung und verriegelten Kassetten-Halbteilen, Fig. 2 eine perspektivisch dargestellte Video-Wendekassette nach Fig. 1 mit auseinandergezogenen Kasset ten-H
albteilen, Fig. 3 eine schematische Draufsicht auf eine Video-Wendekassette mit aus einandergezogenen Kassetten-Halb teilen nach Fig.2, wobei ein Be reich der Kassetten-Halbteile mit aufgebrochener Geh·ausewand ge zeichnet ist und Fig. 4 eine vergr·osserte Darstellung eines des f·ur die Verriegelung der Kas setten-Halbteile vorgesehenen Sperr hakens.
Die Figur 1 zeigt eine perspektivisch dargestellte Video Wendekassette 1 - kurz Kassette genannt - mit einer von der Kassette abgehommenen Abdeckung 2. Die Abdeckung ist f·ur den normalen Verwendungsfall der Kassette in einem tragbaren Videoger·at stets auf der Kassette aufgesetzt und sch·utzt das sonst freiliegende Magnetband 3. Beim Einlegen der Kassette in ein tragbares Videoger·at wird die Abdeckung automatisch seitlich abgeklappt, und das Magnetband ist f·ur den Zugriff von ger·ateseitig vorhandenen Ausziehstiften (nicht gezeichnet) freiliegend. Die Kassette 1 weist die Form eines im wesentlichen quaderf·ormigen K·orpers auf mit zwei darin drehbar gelagerten Magnetband-Wickelspulen 4, 5. An einer schmalen L·angsfl·ache der Kassette ist eine ·Offnung mit teilweise zur·uckgesetzter Geh·ausewand 6 zur freiliegenden Nagnetband- f·uhrung vorgesehen.
Die Kassette selbst besteht aus zwei im wesentlichen geschlossenen Halbteilen 7, 8. Die einzelnen Kassetten-Halbteile 7, 8 bestehen wiederum aus zwei fast vollst·andig geschlossenen Halbschalen, die zusammengeschraubt oder nach einer der sonst bekannten Verbindungsformen haltbar zusammengef·ugt sind. Beide Kassettenhalbteile 7, 8 sind verriegelbar und k·onnen durch Eindringen von zwei Stiften 9, 10 (strichpunktiert gezeichnet) in an der Kassette vorgesehenen F·uhrungsbohrungen 11, 12 gel·ost werden. Die Kassettenhalbteile sind sodann auf einen vorgesehenen Abstand auseinanderzuziehen.
In der Figur 2 ist die Kassette im auseinandergezogenen Zustand gezeichnet. Die Verbindung der beiden verschiebbaren Kassetten-Halbteile 7, 8 erfolgt ·uber zwei flache F·uhrungsteile 13, 14. Die F·uhrungsteile sind parallel und in geringem Abstand zu den ·ausseren schmalen L·angsfl·achen 15, 16 der Kassetten-Halbteile angeordnet. Die Verriegelung der Kassettenhalbteile erfolgt im geschlossenen Zustand der Kassette ·uber die den F·uhrungsseiten zugeordneten Sperrhaken 17, 18. Die beiden F·uhrungsbohrungen 11, 12 zur Entriegelung der Sperrhaken 17, 18 liegen im Teilungsbereich der beiden Kassetten-Halbteile 7, 8 und bestehen somit aus den vier Bohrungsh·alften 11', 11" und 12', 12''.
Aus der Figur 3 sind weitere Einzelheiten ·uber die Ausgestaltung der Sperrhaken und der Lagerung der F·uhrungsteile 13, 14 in den Kassetten-Halbteilen 7, 8 zu erkennen. Die F·uhrungsteile 13, 14 sind in F·uhrungsnuten 19, 20, die sich im Inneren der Kassetten-Halbteile befinden, gelagert. Um sicherzustellen, dass sich die Kassetten Halbteile 7, 8 nicht nur in Haupterstreckungsrichtung (s. waagerechte Pfeilangabe) der Kassette 1 gegeneinander verschieben lassen, sondern auch in begrenzter Weise senkrecht hierzu (s. senkrechte Pfeilangabe) ausweichen k·onnen, sind die F·uhrungsteile 13, 14 aus schmalem Federbandstahl gefertigt.
Die Bandwickelspulen 4, 5 in der ausgezogenen Kassette k·onnen sich somit der Lage der im Heimger·at befindlichen und gegen·uber dem tragbaren Videoger·at unterschiedlichen Antriebselementen voll anpassen. Zur Begrenzung der Auszugsl·ange der Kassette weisen die F·uhrungsteile 13, 14 Begrenzungsnasen 21 auf.
Die Figur 4 zeigt einen vergr·ossert gezeichneten Ausschnitt des Sperrhakens aus einem Kassetten-Halbteil.
Der Sperrhaken 18 besteht aus einem Hakenteil 22, einem Lagerauge 23 und einem Verbindungssteg 24. Eine Druckfeder 25, die auf dem Verbindungssteg des Sperrhakens aufgesetzt ist und sich im Geh·ause des Kassetten-Halbteils abst·utzt, sorgt f·ur den n·otigen Verriegelungsdruck bei zusammengeschobenen Kassetten-Halbteilen. Im verriegelten Zustand beider Halbteile 7, 8 liegt das Sperr haken-Hakenteil 22 des einen Halbteils in einertrSperr- zahn 26 des anderen Halbteils. ·Uber eine Schr·agfl·ache 27, die sich am Sperrhaken-Verbindungssteg befindet, kann ·uber das Auftreffen eines in die Kassette eintauchenden Stiftes 9, 10 die Verriegelung des Sperrhakens aufgehoben werden. Das Hakenteil 22 des Sperrhakens weist in bekannter Weise eine Anlaufschr·age auf ·Uber einen Lagerstift ist der Sperrhaken 18 im Kassetten-Halbteil drehbar gelagert.

a housing, having first and second plane parallel main walls, two side walls connected to the main walls, a rear, and a front having an opening between said main walls,
two adjacent reel hubs rotatably arranged between said main walls;
a length of magnetic tape having respective ends connected to the reel hubs, a portion of said length being stretched along said front opening for cooperation with parts of a magnetic tape apparatus, and
cover means, connected to and pivotable relative to the housing about an axis parallel to said main walls and the cassette front, between a closed position and an open position,
wherein said cover means comprises a single cassette cover arranged to substantially cover the entire front of the housing when in the closed position, and connecting means for pivotally connecting said cover to the housing for movement from the closed position to a first open position by pivoting in a first direction toward the first main wall, and to a second, different open position by pivoting in a second direction toward the second main wall.
2. A cassette as claimed in claim 1, wherein
said cover comprises two pivoting arms having free ends, said arms extending along respective side walls of the cassette housing toward the housing rear when in the closed position, and
said connecting means includes pivotal bearing means disposed midway between said main walls near said free ends, for connecting the cover to said side walls such that the cover is pivotable about a single axis in both directions.
3. A cassette as claimed in claim 1, further comprising resilient means for loading said cassette cover relative to other parts of the cassette, for holding the cover in a stable balanced position in its first and in its second open position for any orientation of the cassette relative to the direction of the force of gravity.
4. A cassette as claimed in claim 1, wherein
said cover comprises two pivoting arms having free ends, said arms extending along respective side walls of the cassette housing toward the housing rear when in the closed position,
said connecting means includes pivotal bearing means disposed midway between said main walls near said free ends, for connecting the cover to said side walls, and
the pivotal bearing means comprises first pivotal bearing means for pivoting the cover in the first direction about a first pivotal axis, and second pivotal bearing means for pivoting the cover in the second direction about a second pivot axis, spaced from the first axis, the first pivotal bearing means and axis being disposed nearer the first main wall, and the second pivotal bearing means and axis being disposed nearer the second main wall.
5. A cassette as claimed in claim 4, wherein
said first pivotal bearing means includes respective first bearing journals disposed on the respective pivoting arms of the cassette cover, the second pivotable bearing means includes second bearing journals disposed on the respective pivoting arms, and the cassette housing includes stops for engaging the second bearing journals to limit the pivotable movement of the cover in its first pivoting direction, and stops to engage the first bearing journals to limit the pivotable movement of the cover in its second pivoting direction.
6. A cassette as claimed in claim 4, wherein
the first pivotable bearing means comprise first bearing journals and parts of the cassette which define first bearing recesses for receiving the first bearing journals, and
the second pivotable bearing means comprises second bearing journals and parts of the cassette which define second bearing recesses for receiving the second bearing journals,
each of said bearing recesses having an opening at its circumference to allow movement of the first bearing journals out of the first bearing recesses when the cover is pivoted about the second pivoting axis, and to allow movement of the second bearing journals out of the second bearing recesses when the cover is pivoted about the first pivoting axis.
7. A cassette as claimed in claim 4, wherein
the bearing journals are disposed on the pivoting arms of the cover,
the housing side walls include arcuate first guide slots, which each terminate in the respective openings in the circumference of the first bearing recesses, for guiding the first bearing journals with play when the cassette cover is pivoted in its second pivoting direction; and second guide slots, which each terminate in the respective openings in the circumference of the second bearing recesses, for guiding the second bearing journals with play when the cassette cover is pivoted in its first pivoting direction,
each of said guide slots having an end remote from the associated bearing recess terminating at a portion of the housing side wall, said side wall portion being one of said stops for limiting pivotable movement of the cover.
8. A cassette as claimed in claim 6, wherein
parts of the cassette define arcuate first guide slots, which each terminate in the respective openings in the circumference of the first bearing recesses, for guiding the first bearing journals with play when the cassette cover is pivoted in its second pivoting direction, and
parts of the cassette define arcuate second guide slots, which each terminate in the respective openings in the circumference of the second bearing recesses, for guiding the second bearing journals with play when the cassette cover is pivoted in its first pivoting direction.
9. A cassette as claimed in claim 8, wherein
the bearing recesses have an at least partly circular cross-section with a diameter equal to the maximum transverse dimension of the associated bearing journal plus the play,
the bearing journals have an elongate shape, with a width dimension which is smaller than the length dimension, and
the arcuate guide slots have a width dimension which is adapted to the width dimension of the associated bearing journal and is smaller than the diameter of the associated bearing recess so as to prevent movements of the cassette cover other than in the first or the second pivoting direction in every position of the cassette cover.
10. A cassette as claimed in claim 9, wherein
said bearing journals are disposed on the pivoting arms of the cover, and the guide slots are located in the housing side walls, and
each side wall of the housing further includes mounting slots extending in the direction of the bearing recesses and intersecting the guide slots at intersections, for mounting the bearing journals in the bearing recesses, said mounting slots each having an open entry side to allow unimpeded entry of the bearing journal into the mounting slot and having a bottom with a profile which extends between a first level at which there is play between the cassette cover and the cassette housing, and a second level at which the cassette cover has an interference fit between the respective bearing journals and the bottoms of the mounting slots.
11. A cassette as claimed in claim 1, each main wall having at least one cut-out which extends to the cassette front, to permit passage of an element of a cassette apparatus behind the stretched portion of the tape and withdrawal of the tape from the housing at the front,
wherein the cassette further comprises first and second slide plates disposed respectively near the first and second main walls, and means for mounting said slide plates to the housing for movement between a closing position nearer the front of the cassette and a retracted position nearer the rear of the cassette, in the closing position each slide plate at least partly closing the respective cut-out openings in the respective main wall, in the retracted position the slide plate being clear of said respective cut-out openings.
12. A cassette as claimed in claim 11, wherein
said two slide plates are parts of a single slide member which is bodily movable between a retracted position and a closing position, said member further including two side walls which extend along the side walls of the cassette housing and which interconnect the slide plates.
13. A cassette as claimed in claim 12, wherein
said slide member consists of a unitary plastic molding.
14. A cassette as claimed in claim 12, wherein
the slide member consists of two identical parts each having snap-connection means for interconnecting said identical parts through a snap connection, each of said identical parts being a unitary plastic molding.
15. A cassette as claimed in claim 12, wherein
said cover comprises two pivoting arms having free ends, said arms being disposed on the outside of the cassette housing, and extending along respective side walls of the cassette housing toward the housing rear when in the closed position, the slide member being arranged such that in the closed position of the cassette cover the slide member side walls cover the pivoting arms.
16. A cassette as claimed in claim 12, comprising resilient means for urging the cassette cover and the slide member toward each other, for holding the cassette cover in a stable balanced position under the influence of the resilient urging in its first and in its second open positions for any orientation of the magnetic tape cassette relative to the direction of the force of gravity.
17. A cassette as claimed in claim 12, wherein
each slide member side wall includes a portion prolonged to the rear of the cassette housing, so arranged that in the closing position of the slide member each side wall of the said member extends beyond the location of rear edges of the side plates when the slide member is in the more retracted position.
18. A cassette as claimed in claim 12, wherein
said slide member and said housing include cooperating stop means for preventing a slide member, mounted on the housing, from sliding off the housing in the absence of the cassette cover.
19. A cassette as claimed in claim 18, wherein
said cooperating stop means are arranged so that when the slide member is in its closing position a portion of said slide member abuts a portion of the cassette housing, and wherein said cassette includes resilient means which act both on the cassette housing and the slide member for urging the slide member toward the closing position, whereby in the closing position said stop means transmits the resilient load from the slide member to the cassette housing.
20. A cassette as claimed in claim 12, wherein
said slide member and said cassette cover include cooperating parts for causing the cassette cover to pivot toward the closed position from either one of the two open positions.
21. A cassette as claimed in claim 20, wherein
the slide member and the cassette cover include cooperating latching means for preventing the cassette cover from moving to a open position when the slide member is in the closing position.
22. A cassette as claimed in claim 21, wherein
each of the side walls of the slide member has an edge remote from the rear of the cassette housing arranged to be clear of the cassette cover, at least at locations disposed near the main walls of the housing, for engagement by an element of a cassette holder when the cassette is inserted into a cassette apparatus, so as to move the slide member to its more retracted position.
23. A cassette as claimed in claim 22, wherein
each of said edges of the slide member side walls includes a notch located midway between the main walls of the housing, and the cassette cover includes lateral projections for engaging the respective notch when the cassette cover is closed.
24. A cassette as claimed in claim 12 wherein,
at the location of the side walls of the slide member when this member is in its more retracted position, each of the side walls of the housing has a curved profile having a radius of curvature substantially equal to the distance between the two housing side walls, so arranged that the slide member may undergo at least limited twisting relative to the cassette housing whereby one side wall of the slide member becomes disposed nearer the rear of the cassette housing than the other slide member side wall, without jamming of the slide member on the housing.
25. A cassette as claimed in claim 12, comprising resilient means for urging the slide plates toward their closing positions, said resilient means acting both on the cassette housing and on the slide plates.
26. A cassette as claimed in claim 25, wherein
said two slide plates are parts of a single slide member which is bodily movable between a retracted position and a closing position, said member further including two side walls which extend along the side walls of the cassette housing and which interconnect the slide plates,
said slide member further including a connecting member halfway between the member side walls, behind the stretched tape portion, and
said resilient means for loading the slide member toward the closing position comprises a pressure spring bearing against the connecting member and the cassette housing.
27. A cassette as claimed in claim 26, wherein said slide member and the connecting member together consist of a unitary plastic molding.
28. A cassette as claimed in claim 26, wherein
the slide member consists of two identical parts each have snap-connection means for interconnecting said identical parts through a snap connection, each of said identical parts being a unitary plastic molding, and
said connecting member is formed by identical parts of said two identical parts.
Description:
BACKGROUND OF THE INVENTION
1. Field of the Invention
The invention relates to a magnetic tape cassette which is adapted to cooperate, in a first position and in a reversed second position, with parts of a cassette recording and/or playback apparatus (hereinafter referred to as a cassette apparatus); and more particularly to a cassette having first and second adjacently disposed reel hubs, which are rotatable about parallel spaced first and second axes of rotation in a cassette housing; a length of magnetic tape having a first end connected to the first reel hub and having a second end connected to the second reel hub, so as to enable it to be wound from the first reel hub to a reel on the second reel hub and back from the second reel hub to a reel on a first reel hub, and having a stretched tape portion along a front opening of the cassette housing for cooperation with parts of a cassette apparatus; and cover means connected to the cassette housing and pivotable relative thereto about a pivoting axis which is parallel to the main walls between a closed position and an open position. In the closed position, the cover extends along the front of the cassette housing, to at least partly cover the stretched portion of the magnetic tape and thus protect the magnetic tape against inadvertent damaging when the magnetic tape cassette is not placed on a cassette apparatus. The open position, when the magnetic tape cassette is placed on a cassette apparatus, allows parts of the cassette apparatus to cooperate with the stretched portion of the magnetic tape.
Magnetic tape cassettes in a variety of versions have gained a high degree of popularity in various fields of application. This may be attributed to the high vulnerability of the magnetic tape medium when not accommodated in a cassette. The magnetic tapes commonly used in magnetic tape equipment for the consumer market and also for many semiprofessional and professional uses have a thickness dimension which is very small in comparison with the width dimension. The thickness dimensions generally range between 15 and 40 um, while the width for the more customary magnetic tapes varies roughly between 12 and 25 mm. The magnetic tapes consist of a plastic foil which on one side is provided with a finely dispersed magnetizable material, and has an extremely high degree of flexibility. The magnetic tape cassette affords protection against damaging of the delicate and vulnerable magnetic tape, so that the ease of handling the magnetic tape medium is substantially improved.
For many simple applications it suffices if the front of the cassette is at least partly closed and is provided with openings for the passage into the cassette of parts of a cassette apparatus, such as a recording/playback head, an erase head and a pressure roller. Such a cassette is for example the so-called Compact Cassette, also referred to as the Philips cassette, which is generally used for audio purposes. With this cassette the magnetic tape need never be removed from the housing, so that the front may be partly closed and thus affords adequate protection of the magnetic tape against inadvertent touching. While dust can reach the magnetic tape through the openings, this seldom presents a problem in that tape application.
Still other known cassettes are intended for use with a cassette apparatus which includes a device for partly withdrawing the magnetic tape from the cassette housing and bringing the portion of the magnetic tape thus removed from the cassette housing into contact with the magnetic heads. For audio applications this enables a better guidance of the magnetic tape during its transport from the one reel to the other along the magnetic heads to be obtained, so that higher quality standards in respect of signal recording and reproduction can be achieved than with the previously mentioned Compact Cassette, in which the lace-up is determined by components of the cassette housing.
In known magnetic video tape equipment for home-entertainment use, which to date are always equipped with rotary magnetic heads which write obliquely oriented closely spaced tracks on the magnetic tape, the magnetic tape should also be withdrawn from the cassette housing. The front of the cassette housing must then be free of wall portions which could interfere with the withdrawal of the magnetic tape from the cassette housing. As a result of the absence of wall portions at the front the likelihood of the magnetic tape being touched inadvertently increases. This likelihood is further increased because the cassette apparatus customarily includes a device for withdrawing the magnetic tape from the cassette housing. Such a device enters the cassette housing through the main walls behind the magnetic tape and should engage the back side of the magnetic tape during withdrawal. Therefore, cut-outs which extend to the front are necessary in the main walls of the cassette. These cut-outs expose the edges of the magnetic tape, which exposure greatly increases the likelihood of the magnetic tape being damaged.
Another aspect of cassette design is that, when magnetic tape cassettes are used on equipment which enables higher quality audio recording and reproduction or which enables video signals to be recorded and reproduced, dust should be prevented from reaching the magnetic tape as far as possible, because dust may affect the high quality of recording and reproduction.
Therefore many magnetic tape cassettes are provided with movable cover means in order to protect the stretched portion of the magnetic tape which extends along the fro
2. Description of the Prior Art
Magnetic tape cassettes which are suitable for use on a cassette apparatus in a first position only and which are consequently not suitable for cooperating with the apparatus in a reversed or "flipped over" second position, so-called non-reversible cassettes, present fewer problems in respect of the protection of the magnetic tape, because only one of the two main walls need be provided with cut-outs for withdrawal of the magnetic tape from the cassette. Such a cassette is for example known from U.S. Pat. No. 3,900,172. A cassette cover closes the front of the cassette housing if the cassette is removed from a cassette apparatus. On its side which faces the rear of the cassette the cassette cover has an additional ridge which covers the back side of the magnetic tape when the cassette cover is closed. Although one of the main walls of the cassette has a comparatively large opening this still provides satisfactory protection of the magnetic tape. However, dust can still rather easily reach the magnetic tape, and the tape can readily be damaged by the ridge if the stretched portion of the magnetic tape in the cassette is not sufficiently taut.
In the case of reversible magnetic tape cassettes this solution cannot be adopted. If the housing of a reversible magnetic tape cassette has cut-outs in the main walls for withdrawal of the magnetic tape from the magnetic-tape cassette, the cut-outs should be formed in both main walls. From German Offenlegungsschrift No. 2,552,063, to which U.S. Pat. No. 4,021,006 corresponds, a reversible magnetic tape cassette of this type is known, having two cassette covers which partly extend along the front of the cassette housing: a first cassette cover on the side near the first main wall of the cassette housing, and a second cassette cover on the side near the second main wall of the
When this known magnetic-tape cassette is placed on a cassette apparatus, a unit on the deck of the cassette apparatus partly opens the two cassette covers, after which the magnetic heads are brought into contact with the magnetic tape through the slot between the two cassette covers. The magnetic tape cassette has cut-outs in the main walls for bringing the magnetic tape into contact with two pressure rollers by means of two capstans on either side of the magnetic head, which capstans are situated behind the magnetic tape.
A disadvantage of this known cassette is that both in the first and in the second position of the magnetic tape cassette on a cassette apparatus the two cassette covers must be opened. One of the two cassette covers is then always pivoted into a position in which it moves toward and faces the cassette apparatus. In the cassette apparatus the magnetic tape cassette should therefore be supported in such a way that there is sufficient clearance between the main wall of the magnetic tape cassette which faces the cassette apparatus and the parts of the apparatus near that wall. Another drawback is that the opened cassette covers constitute an obstruction to the device which withdraws the magnetic tape from the cassette, unless the cassette covers are opened very far. This last alternative demands a still greater clearance. Otherwise both sides adjacent the cassette covers must have cut-outs formed which open towards the front, as in the known cassette, so that the magnetic tape is exposed at these locations. The spaced required above the cassette for the opened cassette cover is comparatively large, because the cassette cover portion which is disposed in the main wall also pivots upwards. This is a drawback because the overall height of a cassette apparatus should be minimized for obvious reasons.
Therefore, the known magnetic tape cassette is less suitable for application where the magnetic tape is to be withdrawn from the cassette housing. Moreover, unless openings are formed in the main walls of the cassette housing on both sides of the cassette covers for the passage of the tape withdrawal elements of a cassette apparatus, which means that there will be locations on both sides of the cassette covers where the magnetic tape can be touched and damaged, the two cassette covers should be pivoted into their open positions before the magnetic tape cassette is moved to an operating position over the withdrawal elements of the cassette apparatus. However, for thus swinging open the cassette covers before the magnetic tape consists is completely in its operating position, the known magnetic tape cassette is less suitable because of the actuation elements for the cassette covers which are then required. Further, the part of the cassette cover which faces the deck of the cassette apparatus and which is situated at the front of the cassette housing constitutes an obstruction for the withdrawal elements even if the cassette covers are swung open very far.
SUMMARY OF THE INVENTION
It is the object of the invention to provide a magnetic tape cassette which may be inverted or flipped over, and which provides good protection against dust or accidental touching when closed, but does not require excessive clearance between the cassette and the apparatus.
Covers
In accordance with the invention a single cassette cover substantially covers the entire front of the cassette housing; and on both sides the cassette cover is provided with pivoting arms which extend along the side walls of the cassette housing toward the rear of the cassette housing in the closed position, from its closed position the cassette cover being pivotable into either of two different open positions, one towards the first main wall of the cassette housing and the other towards the second main wall of the cassette housing.
In the cassette in accordance with the invention the entire front of the cassette housing is covered, so that if the main walls have cut-outs which extend to the front of the cassette housing, the tape is protected to some extent against inadvertent touching. As the cassette cover is movable in either of two pivoting directions, a magnetic tape cassette is obtained which on its side which faces a cassette apparatus has no obstacles which impair placing of the cassette on the cassette apparatus or the insertion of elements of the apparatus into the cassette. Above the magnetic tape cassette a certain clearance is required for the swung-open cassette cover. However, this clearance may be comparatively small and need not be greater than the height dimension of the magnetic tape cassette, but may even be smaller.
In most cassette equipment, the magnetic tape cassette is not placed directly onto the deck by hand, but is slid into a movable cassette holder, after which the cassette holder is moved towards the deck. The magnetic tape cassette in accordance with the invention is particularly suitable for such applications, because the movement of the magnetic tape cassette towards the deck allows provisions to be made on the deck for opening the cassette cover during the movement of the cassette holder. The cassette cover which is thus opened during the movement of the cassette holder does not impede insertion into the magnetic tape cassette of elements such as capstans, pressure rollers, magnetic tape retaining elements or elements for withdrawing the magnetic tape from the cassette.
Single Pivot
In a simple embodiment of the invention pivotal bearing means are disposed midway between the first and the second main wall and the cassette cover is pivotable in its first and its second pivoting directions about a single pivoting axis midway between the two main walls. This embodiment reduces the likelihood of the cassette cover touching the portion of the magnetic tape which is tensioned along the front of the magnetic tape cassette, during the pivotal movement of the cover, if the pivoting axis is situated somewhat to the rear of the magnetic tape cassette.
Double Pivot
In a preferred embodiment of the invention the pivotal bearing means comprise a first pivotal bearing means disposed nearer the side of the first main wall for pivoting the cassette cover in its first pivoting direction about a first pivoting axis which is also nearer the side of the first main wall, as well as a second pivotal bearing means disposed nearer the side o
Bearing constructions which enable a component to be pivoted into two different pivoting directions about two different parallel pivoting axes are known. Examples of these are the known hinge construction for swing doors, while there are also constructions comprising crosswise arranged straps.
A simple bearing construction which is suitable for a magnetic tape cassette is obtained with an embodiment of the invention in which the first pivotal bearing means include fist bearing journals as well as parts of the magnetic tape cassette which define first bearing recesses which receive the first bearing journals, and the second pivotal bearing means include second bearing journals as well as parts of the magnetic tape cassette which define second bearing recesses which receive the second bearing journals. These bearing recesses each have an opening at their circumference to allow movement of the first bearing journals out of the first bearing recesses during pivotal movement of the cassette cover about the second pivoting axis, and to allow movement of the second bearing journals out of the second bearing recesses during pivotal movement of the cassette cover about the first pivoting axis.
In this embodiment it is necessary to prevent the cassette cover in its closed or swung open positions, or during its pivotal movement, from becoming detached from the cassette housing by movement of the bearing journals out of the bearing recesses. In a further preferred embodiment parts of the magnetic tape cassette define arcuate first guide slots which each terminate in the respective openings in the circumference of the first bearing recesses, for guiding the first bearing journals with play during the pivotal movement of the cassette cover in its second pivoting direction; and parts of the magnetic tape cassette define arcuate second guide slots which each terminate in the respective openings in the circumference of the second bearing recesses, for guiding the second bearing journals with play during the pivotal movement of the cassette cover in its first pivoting direction. These parts of the magnetic tape cassette consist of parts of the side walls of the cassette housing if the bearing journals are disposed on the pivoting arms of the cassette cover, or consist of parts of the pivoting arms if the bearing journals are disposed on the side walls of the cassette housing.
The two guide slots intersect each other midway between the two main walls of the cassette housing. At the location of the intersection there is a possibility that a bearing journal does not move in the corresponding guide slot, so that the cassette cover could assume a wrong position. It is therefore advantageous to use an embodiment in which the bearing recesses have an at least partly circular cross-section with a diameter equal to the maximum transverse dimension of the associated bearing journal plus the play; the bearing journals have an elongate shape with a width dimension which is smaller than the length dimension; and the arcuate slots have a width dimension which is adapted to the width dimension of the associated bearing journal and is smaller than the diameter of the associated bearing recess. This embodiment prevents movements of the cassette cover other than in the first or the second pivoting direction in every position of the cassette cover, by cooperation of the bearing journals and parts of the cassette housing.
If the bearing journals are disposed on the pivoting arms and the guide slots are disposed in the side walls of the cassette housing, in another preferred embodiment providing a simple mounting of the cassette cover, each side wall of the cassette housing has mounting slots which extend in the direction of the bearing recesses and which intersect the guide slots at intersections, for mounting the bearing journals in the bearing recesses. The mounting slots each have an open entry side to allow unimpeded entry of the bearing journal into the mounting slot, and furthermore have a bottom with a profile which extends from a level at which there is play between the cassette cover and the cassette housing to a level at which the cassette cover is slightly bent by an interference fit between the bearing journals and the bottom of the mounting slots. Thus, when the cassette cover is being mounted, the cassette cover is slightly bent until the bearing journals engage with the bearing recesses, after which the bearing journals snap into the bearing recesses as a result of the resilient action of the cassette cover itself.
In order to obtain well-defined open positions of the cassette cover in a magnetic tape cassette of the types described above having first and second pivoting axes, according to another preferred embodiment of the invention in which the bearing journals are disposed on the pivoting arms of the cassette cover, the cassette housing is provided with stops which are adapted to cooperate with the second bearing journals so as to limit the pivotal movement of the cassette cover in its first pivoting direction, and with stops which are adapted to cooperate with the first bearing journals so as to limit the pivotal movement of the cassette cover in its second pivoting direction. In the embodiment in which guide slots for the bearing journals are formed in the side walls of the magnetic tape cassette, each of the guide slots at its end which is remote from the corresponding bearing recess may terminate at a portion of the side wall of the cassette housing, which portion functions as one of the stops which is adapted to cooperate with the bearing journals so as to limit the pivotal movements of the cassette cover.
Slide Plates
The invention is suitable both for audio and for video cassettes, both when they are not provided with cut-outs in the main walls which are open towards the front of the cassette housing and when such cut-outs are provided. However, it is a further object of the invention to provide a magnetic tape cassette having maximum fields of application. For such an objective it is necessary to form large cut-outs in the main walls of the cassette housing to permit the passage of elements of cassette apparatus of different types. In the case in which large cut-outs in the main walls of the cassette housing extend to the front, there is an increased risk of the magnetic tape being damaged and of dust and dirt penetrating into the interior of the cassette.
An embodiment of the invention, which satisfies this object, includes a first and a second slide plate respectively disposed near the first and second main walls, each slide plate being movable between a retracted position nearer the rear of the cassette housing and a closing position nearer the front of the cassette housing. Each slide plate leaves the respective openings in the corresponding main wall clear in its retracted position, and closes these openings at least partly and preferably completely in the closing position. Thus it is possible to provide magnetic tape cassettes which, once they have been removed from the cassette apparatus, are almost completely closed, except of course for the openings in the main walls for the passage of drive spindles for the magnetic tape reels; but which, once they have been placed on a cassette apparatus, first of all have a fully open front, and secondly also provide satisfactory access behind (to the back side of) the magnetic tape to allow passage of elements of a cassette apparatus through the cut-outs in the main walls.
An embodiment is preferred in which the two slide plates are part of a single slide member which is bodily movable between the retracted position and the closing position, which member also includes two side walls which extend along the side walls of the cassette housing and which interconnect the slide plates. The slide member may then be formed as a unitary component which is integrally manufactured from a plastic. These embodiments have the advantage that easy guidance and journalling of the slide plates on the cassette housing is assured.
Alternatively, according to another preferred embodiment, the slide member comprises two identical parts which are integrally manufactured from a plastic, which parts are provided with snap-connection means and are interconnected thereby through a snapped connection. As the two parts of the slide member are identical only one tool is required for manufacturing the slide member. The advantage of this embodiment mainly resides in the simplified mounting of the slide member. By using the snapped connection, the member can readily be mounted on the cassette housing after the magnetic tape reels and the cassette cover have been mounted in and on the cassette housing respectively. If the two pivoting arms of the cassette cover are located on the outside of the cassette housing, in a still further preferred embodiment the side walls of the slide member cover the pivoting arms in the closed position of the cassette cover. Thus, the pivoting arms are well protected when the magnetic tape cassette is removed from a cassette apparatus, so that the comparatively vulnerable bearing means of the cassette cover are protected against mechanical dam
Spring Restraints
For specific uses of the magnetic tape cassette in accordance with the invention it may be of importance that, once a cassette cover is open, it does not swing back to its closed position under the influence of gravity. An embodiment of the invention which is of interest in this respect includes resilient means which load the cassette cover relative to other parts of the magnetic tape cassette, the cassette cover being in a stable balanced position under the influence of the resilient load in its first and in its second open position for any orientation of the cassette relative to the direction of the force of gravity. The resilient means may for example act on the cassette cover and on the slide member and urge these components towards each other. Leaf spring constructions are also possible which cooperate with non-round bearing journals of the cassette cover. However, it is not always desirable to subject the cassette cover to a resilient load, because the bistable positions which the cassette cover can assume under the influence of the resilient menas require that the cassette apparatus include means for closing the cassette cover against the resilient load.
Comparatively simple means on the cassette apparatus are sufficient for moving the slide plates. Since the slide plates slide over the main walls of the cassette housing they are easily opened during the operation of inserting the magnetic tape cassette into a cassette holder. Preferably, resilient means are provided which act both on the cassette housing and on the slide plates so as to urge the slide plates towards their closing positions. With the aid of these resilient means the slide plates are always automatically moved towards their closed positions when the magnetic tape cassette is removed from the cassette apparatus. Moreover, the resilient means enable automatic ejection or at least partial ejection of a magnetic tape cassette from a cassette holder.
Accommodating the resilient means in the magnetic tape cassette may be a problem in view of the limited space which is available. When a slide member which is bodily movable is used, an embodiment is therefore of interest which makes optimum use of the space available in a magnetic tape cassette. In this embodiment the first and the second slide plates of the slide member are interconnected halfway between its two side walls and behind the magnetic tape by means of a connecting member, and the resilient means for loading the slide member towards the closed position comprise a pressure spring between the connecting member and the cassette housing. Thus, in the cassette housing a space exists halfway between its side walls and between the two circular reels, which can readily accommodate a helically wound pressure spring, so that the available and generally unused room can be utilized. A further advantage of this embodiment is that owing to the connection between the two slide plates at a location between the two side walls of the slide member the slide member is given a higher rigidity. If the slide member consists of a unitary component which is integrally manufactured from a plastic, it is advantageous to manufacture the slide member and the connecting member together as a single integrally manufactured component. As the connecting member is located behind the magnetic tape, mounting of such a slide member may be difficult. In an embodiment which overcomes this problem the unit comprising the slide member and the connecting member is made of two identical parts which are integrally manufactured from a plastic and provided with snap-connection means, the parts being interconnected by a snapped connection. After the magnetic tape reels have been mounted in the cassette housing and, as the case may be, also after mounting the cassette cover, the slide member can be fitted onto the cassette housing by moving the two parts of the slide member towards each other in a direction perpendicular to the main walls of the cassette housing and interconnecting them by means of a snapped connection. Subsequently, the pressure spring can be mounted between the cassette housing and the slide member.
Cover/Slide Movement
When a bodily movable slide member is used, in yet another preferred embodiment the slide member and the cassette cover are provided with cooperating parts for pivoting the cassette cover towards its closed position, no matter which of its two open positions the cassette cover occupies. The advantage of this embodiment is that the movement of the slide member to its closing position and the pivotal movement of the cassette over from an open position to its closed position can proceed in a single operation, when the slide member is moved towards its closing position. Furthermore, it is advantageous if the slide member and the cassette cover are provided with cooperating latching means which prevent the cassette cover from moving to the open position when the slide member is in the closing position. Thus, the cassette cover will always stay closed as long as the slide member is in its closing position.
For moving the slide member and subsequently opening the cassette cover when the magnetic tape cassette is placed on the cassette apparatus, in yet another preferred embodiment the edge of each of the side walls of the slide member remote from the rear of the cassette housing is arranged to be clear of the cassette cover, at least at locations which are disposed near the main walls. This edge may then be used as a stop means for moving the slide member to its retracted position when the magnetic tape cassette is placed in a cassette holder of the cassette apparatus. For opening the cassette cover after the cassette has been inserted and for moving the slide member in the cassette holder, in a different preferred embodiment the corresponding edge of each of the side walls of the slide member which is remote from the rear of the cassette housing has a recess formed at a location midway between the main walls of the cassette housing. The cassette cover is then provided with lateral projections which engage the recesses when the cassette cover is closed. These projections may be used to open the cassette cover by engaging elements on a cassette apparatus during movement of the cassette holder to an operating position.
In a magnetic tape cassette in accordance with the invention each of the slide plates will have a length dimension which is roughly equal to the distance between the side walls of the cassette housing; and transverse thereto, a width dimension which is substantially smaller. This occurs because the width dimension must be limited so that when the slide plate is in its retracted position the plate does not interfere with the drive means for the magnetic tape reels. The comparatively great length/width ratio of the slide plates is apt to cause the plates to jam if a slide plate or a slide member does not perform a purely translational movement between its closing position and its retracted position, but rather twists slightly about an axis parallel to the axes of rotation of the magnetic-tape reels. Since jamming of the slide plates or the bodily movable slide member is obviously undesirable, in another preferred embodiment of the invention each of the side walls of the cassette housing, at the location of the side walls of the slide member when this member is in its retracted position, is provided with a curved profile with a radius of curvature which is substantially equal to the distance between the two side walls of the cassette housing. This profile enables the slide member to twist a little relative to the cassette housing, such that one side wall of the slide member is nearer the rear of the cassette housing than the other side wall of the slide member, without the slide member becoming jammed on the cassette housing.
In a different embodiment which is adapted to eliminate jamming effects, each of the side walls of the slide member comprises a portion which protrudes towards the rear of the cassette housing, so arranged that in the closing position of the slide member each side wall of the slide member extends beyond the location occupied by those sides of the slide plates of the slide member facing the rear of the cassette housing when the slide member is in its retracted position. That lo
In many cases, especially if the slide member is loaded towards its closing position by resilient means, it is advantageous if the slide member and the housing are provided with cooperating stop means to prevent a slide member, once it has been mounted, from sliding off the cassette housing when the cassette cover has not yet been mounted or has been removed. This embodiment provides greater ease of handling the magnetic tape cassette during assembly. In addition, if the cassette includes resilient means for loading the slide member towards the closing position, a further advantage is obtained from this embodiment if, while the slide member is in the closing position, the stop means engage the slide member and transmit at least the greater part of the resilient load imposed by the resilient means to the cassette housing. When this embodiment is used the cassette cover, and thus the bearing means for the pivotal movements of the cassette cover, are not loaded by the resilient means.
BRIEF DESCRIPTION OF THE DRAWING
The invention will now be described in more detail with reference to the drawing, in which:
FIG. 1 is a view at a first main surface of a magnetic tape cassette having a cassette cover which is pivotable about a single axis,
FIG. 2 is a side view at the cassette cover of the magnetic tape cassette in accordance with FIG. 1,
FIG. 3 is a view at a second main surface of the cassette of FIG. 1.
FIG. 4 is a side view of the magnetic tape cassette in accordance with the preceding Figures,
FIG. 5 is a detail of FIG. 4, showing the cassette cover swung open in a first pivoting direction, and a dashed line showing the cassette cover in a second open position in a second pivoting direction,
FIG. 6 is a view similar to FIG. 1, but of a magnetic tape cassette having a cassette cover pivotable about two pivoting axis and a slide member for closing the openings in the main walls,
FIG. 7 is a front view of the magnetic tape cassette of FIG. 6,
FIG. 8 is a view in accordance with FIG. 6, but now at a different main surface of the magnetic tape cassette,
FIG. 9 is a perspective view of the cassette in accordance with FIGS. 6 to 8, the slide member being in its closing position and the cassette cover being in its closed position,
FIG. 10 is similar to FIG. 9, but with the slide member in its retracted position and the cassette cover opened in a first pivoting direction,
FIG. 11 is similar to FIG. 10, but with the cassette cover opened in a second pivoting direction,
FIG. 12 is a partial exploded view of a magnetic tape cassette in accordance with FIGS. 6 to 11,
FIG. 13 shows a detail of one of the side walls of the cassette in accordance with FIGS. 6 to 12, the position of the bearing journals being shown relative to the bearing recesses and the guide slots when the cassette cover is closed,
FIG. 14, shows the same detail as FIG. 13, but with the cassette cover opened in a first pivoting direction,
FIG. 15 is a sectional view in accordance with the arrows XV--XV in FIG. 14,
FIG. 16 is a cross-section across the center of the slide member and in accordance with the arrows XVI--XVI in FIG. 12,
FIG. 17 is a partial cross-section in accordance with the arrows XVII--XVII in FIG. 16,
FIGS. 18, 19 and 20 are views of a connecting member for interconnecting the slide plates of the slide member in the magnetic tape cassette in accordance with FIGS. 6 to 12,
FIG. 21 shows an integrally manufactured plastic version of a slide member for a magnetic tape cassette in accordance with FIGS. 6 to 12,
FIG. 22 shows a slide member consisting of two plastic components which have been snapped together for the magnetic tape cassette in accordance with FIGS. 6 to 12,
FIG. 23 shows a detail of one of the snap connections for interconnecting the parts of the slide member in accordance with FIG. 22,
FIG. 24 and FIG. 25 illustrate the principle of an embodiment in which a slide member and a cassette cover are loaded relative to each other by means of a tension spring, FIG. 24 representing the situation with the cassette cover closed and FIG. 25 the situation with the cassette cover open,
FIG. 26 is similar to FIG. 8, but with the slide member in a twisted position,
FIG. 27 is a similar view as in FIG. 9 of a modified embodiment, with a slide member which has portions protruding towards the rear of the cassette housing,
FIG. 28 is a view at a main wall of the magnetic tape cassette in accordance with FIG. 27,
FIG. 29 schematically shows a part of a cassette apparatus with a hinged cassette holder containing a cassette in accordance with the invention, the slide member being moved into its more retracted position during insertion of the cassette, and
FIG. 30 is similar to FIG. 29, but with the cassette holder in its operating position and the cassette cover being opened by means provided on the deck of the cassette apparatus.
DESCRIPTION OF THE PREFERRED EMBODIMENTS
Single Pivot

A cassette cover 30 is connected to the cassette housing and is pivotable relative thereto about a pivoting axis 31 parallel to the main walls, between a closed position, shown in FIGS. 1 to 4, and an open position which is obtained by a pivotal movement in a pivoting direction towards a main surface of the cassette housing. The cassette cover covers substantially the entire front opening 20 of the cassette housing.
On both sides the cassette cover is provided with pivoting arms 32 and 33 having free ends 34 and 35 respectively, the arms extending along the respective side walls 14 and 15 of the cassette housing, toward the housing rear when in the closed position. The pivoting arms have free ends 34 and 35 respectively which face the rear 16 of the cassette housing in the closed position. The side walls 14 and 15 of the cassette housing and the pivoting arms 32 and 33 of the cassette cover 30 are provided with pivotal bearing means which cooperate with each other near the free ends 34 and 35 of the pivoting arms 32 and 33. As is shown in FIG. 5 the cassette cover 30 is pivotable from its closed position into two different opened positions. Solid lines in FIG. 5 represent a first open position of the cassette cover 30, which is reached by pivoting the cassette cover in a first pivoting direction indicated by an arrow 36 towards the first main wall 8 of the cassette housing. Dashed lines represent a second open position of the cassette cover reached by pivoting the cassette cover in a second pivoting direction in accordance with an arrow 37 towards the second main wall 9. The main wall 8 has slots 38 and 39 which are open towards the front 20 of the cassette housing for the passage of the pivoting arms 32 and 33 when the cassette cover 30 is pivoted in its first pivoting direction 36. The main wall 9 has corresponding slots 40 and 41 for pivoting in the second pivoting direction 37. The bearing means for the pivotal bearing of the cassette cover comprise two bearing journals 42 and 43 near the free ends 34 and 35 of the pivoting arms 32 and 33 and corresponding recesses in the side walls 14 and 15 of the cassette housing. An example of such a recess is the recess 44 in FIGS. 4 and 5.
The bearing journals 42 and 43 have a square cross-section and the recess 44 as well as the corresponding recess, not shown, in the side wall 15 of the cassette housing has a semicircular cross-section. In the side walls at the location of the bearing journals 42 and 43 leaf springs 45 provide a simple spring restraint for loading the bearing journals towards the rear 16 of the cassette housing. Because of the resilience of the leaf springs loading the square cross-section of the bearing journals of the cassette cover, the cassette cover will be held in a stable balanced position, both in its closed position and in its two open positions for any orientation of the magnetic tape cassette relative to the direction of the force or gravity.
Double Pivots
FIGS. 6 to 20

A cassette cover 66 substantially covers the entire front 63 of the cassette housing. On both sides the cover 66 has pivoting arms 67 and 68 which extend along the sides walls 60 and 61 and which have free ends 69 and 70. In the closed position the arms 67 and 68 extend toward, and the free ends face, the rear 62 of the cassette housing. The side walls 61 and 62 and the pivoting arms 67 and 68 have cooperating pivotal bearing means near the free ends 69 and 70 of the pivoting arms. The cassette cover 66 is pivotable from its closed position, see FIGS. 6 to 8, into two different open positions; namely, a first open position, by pivoting in a first pivoting direction 71 (FIG. 10) towards the first main wall 54, and a second open position, by pivoting in a second pivoting direction 72 (FIG. 11) towards the second main wall 55 of the cassette housing.

Each of the bearing recesses has an opening at its circumference, for moving the bearing journals 75 and 76 out of the corresponding bearing recesses when the cassette cover is pivoted about the second pivoting axis 74 and for moving the bearing journals 78 and 79 out of the corresponding bearing recesses when the cassette cover 66 is pivoted about the first pivoting axis 73.
Actuate first guid

As is in particular apparent from FIGS. 13 to 15 the bearing recesses 77 and 80 have, as shown, an at least partly circular cross-section with a diameter equal to the length (maximum transverse dimension) L of the associated bearing journals 75 or 78 plus some play. The bearing journals have an elongated shape with a width dimension T which is smaller than the length dimension L. The arcuate guide slots have a width dimension W which is adapted to the width dimension T of the associated bearing journal and which is smaller than the diameter of the associated bearing recess. In this way movements of the cassette cover 66 other than in the first or the second pivoting directions 71 and 72 are prevented in any position of the cassette cover by cooperation of the bearing journals and the parts of the side walls 60 and 61 which surround the bearing recesses. The bearing journals are also arcuate, so that they always engage with the associated guide slots in a comparatively accurate manner.
The side walls 60 and 61 also have mounting slots 83 to 86 for mounting the bearing journals in the bearing recesses. FIGS. 13 and 14 show that the mounting slots 83 and 84 respectively intersect the guide slots 82 and 81 at the location of the intersections C1 and C2 respectively. The mounting slots each have an open entry side for the free entry of the bearing journal into the mounting slots. The bottom of each mounting slot has a profile which extends between a level N1 at which there is play between the cassette cover 66 and the cassette housing, and a level N2 at which the cassette cover is slightly bent by forces between the bearing journals and the bottoms of the mounting slots. As is apparent in particular from the detailed section view (FIG. 15) of the slots shown in FIG. 14 t

In order to limit the pivotal movements of the cassette cover 66 the side walls 60 and 61 of the cassette housing are provided with stops which cooperate with the bearing journals. It can be seen from FIGS. 13 and 14 that the guide slots 82 and 81 are closed at the ends 87 and 88 which are remote from their respective bearing recesses 80 and 77. At these locations ungrooved portions of the side walls 60 and 61 of the cassette housing constitute stops for the bearing journals.
Both main walls 54 and 55 of the magnetic tape cassette 47 have cut-outs 89 and 90 which extend to (open towards) the front opening of the cassette housing for the pasage of elements of a cassette apparatus behind the stretched tape portion 65. In order to minimize the penetration of dust into the magnetic tape cassette, even when the cassette cover is open, the cassette is provided with a closed front wall 91 at the rear of the cut-outs 89 and 90. The wall 91 has two openings 92 and 93, at a location of two tape guide rollers 94 and 95 respectively, just large enough to permit withdrawing the magnetic tape 64.
Slide Plates
Near the first and near the second main wall there are respectively located a first slide plate 96 and a second slide plate 97, which are slidable between a retracted position (FIGS. 10, 11) nearer the rear 62 of the cassette housing and a closing position (FIGS. 6-9) nearer the front 63 of the cassette housing. In the retracted position the slide plates 96 and 97 leave the cut-outs 89 and 90 in the corresponding main walls 54 and 55 free. In the closed position the cut-outs are completely closed.
The two slide plates 96 and 97 form part of a single slide member 98 (hereinafter referred to as slide 98) which is bodily movable between a retracted position (see FIGS. 10 and 11) and a closing position (see FIGS. 6 to 9). The slide 98 includes the two slide plates 96 and 97 as well as two side walls 99 and 100 which extend along the side walls 60 and 61 of the cassette housing and which interconnect the slide plates.

In this preferred embodiment, the slide 98 is manufactured from a plastic as a unitary molding. It is alternatively possible to use a two-part slide 101 as shown in FIG. 22, which comprises slide plates 102 and 103 and side walls 104 and 105. This slide comprises two identical unitary molded plastic parts, the one part comprising the slide plate 102 and the side wall 104 and the other part the slide plate 103 and the side wall 105. The parts are connected to each other by means of snap connections. FIG. 23 shows a cross-section across the snap-connection means, which connect the slide plate 102 to the side wall 104. The connection means comprise a pin 106 with a thickened frustoconical upper end 107. At the location of the pin 106 the slide plate 102 has a hole 108, and counterbore 109 which receives the conical end 107 of the pin 106. This conical end has a diameter which is slightly larger than the hole 108, so that when the slide plate 102 is mounted on the side wall 104 the conical end is slightly elastically deformed as it passes through the hole 108 until the counterbore 109 is reached. The slide 101 operates in an identical manner as the slide 98.
In the magnetic tape cassette 47 the two pivoting arms 67 and 68 of the cassette cover 66 are located outside the cassette housing. When the slide 98 is in its closing position the arms 67 and 68 are covered by the side walls 99 and 100 of the slide, so that when the magnetic tape cassette is removed from a cassette apparatus the pivoting arms and thus the bearing means are satisfactorily protected against mechanical damage. Moreover, a clean-cut appearance is thus obtained.
Spring Restraint
The complete slide 98 is loaded towards its closing position by a pressure spring 110 (FIGS. 6 and 8). For this purpose the slide plates 96 and 97 are interconnected by a connecting plate 111 halfway between the side walls 99 and 100, behind the stretched tape portion 65. The pressure spring 110 is fitted around a pin 112 extending rearward from the plate 111, and bears against the connecting plate 111 and against the bottom of a blind hole 113 in the cassette housing midway between its side walls 60 and 61 (FIG. 12). The connecting member, also see FIGS. 18 to 20, not only serves as a point of attachment for the pressure spring 110, but also stiffens the slide 98. Without this stiffening, the comparatively thin slide plates 96 and 97 can readily be bent. The connecting plate 111 has two slots 114 and 115 which engage two ridges 116 and 117 on the rear center of the slide plates 96 and 97.
Instead of a slide 98 with a separate connecting plate 111, it is alternatively possible to employ a slide 118 which is integrated with a connecting plate 119, as shown in FIG. 21. The slide plates 120 and 121, as well as the side walls 122 and 123, the connecting plate 119 and the pin 124 extending from the plate are integrally manufactured from a suitable plastic by injection molding. When such a slide is used the various components of the cassette must be assembled in such a sequence that the stretched tape portion 65 along the front of the cassette does not obstruct fitting of the slide. In order to facilitate the mounting of the pressure spring a pin may be used which is substantially shorter then the pin 124. Instead of the pin a local recess in the surface of the connecting plate may be used in order to prevent undesired lateral movements of the end of the pressure spring.
The two-part slide 101 in accordance with FIG. 22 enables the slide to be mounted after the magnetic tape has been placed in the cassette housing. This slide comprises a connecting plate 125 consisting of two parts 125A and 125B, which are integral with the slide plate 102 and the slide plate 103 respectively. The part 125B is connected to the slide plate 102 by a snap connection of the type of FIG. 23 and the part 125A is connected to the slide plate 103 by means of a similar snap connection. The pin 173 also consists of two parts, but is otherwise the same as the pin 124 described in the preceding paragraph.
Cover/Slide Movement
The pressure spring 110 ensures that the slide 98 is normally in its closing position when the cassette is not placed on a cassette apparatus, and thus covers the openings 89 and 90 in the main walls of the cassette housing. In its closing position the slide also covers any other openings in the main walls, such as the customary locating openings 126 to 129 (FIGS. 6 and 8) for locating the cassette relative to a cassette apparatus with the aid of locating pins provided on the deck of the apparatus. However, the pressure spring 110 also has another function, namely the closure of the cassette cover 66 when the slide 98 is moved to its closing position. For this purpose the slide 98 and the cassette cover 66 are provided with cooperating parts which cause the cassette cover to pivot to its closed position from either of its two open positions. As shown in FIGS. 10 and 11, the edges of the pivoting arms 67 and 68 and parts of the slide plates 96 and 97 engage in a sliding fashion to provide this cooperation.
The slide 98 and the cassette cover 66 are provided with a cooperating latch for preventing the cassette cover 66 from moving to an open position if the slide 98 is in its closing position, so that a magnetic tape cassette which has been removed from an apparatus cannot readily be opened. This is possible only after at least partly moving back the slide 98 toward its retracted position against the force of the pressure spring 110. The latching means again are formed by the edges of the pivoting arms 67 and 68 of the cassette cover 66 and parts of the slide plates 96 and 97 of the slide 98, namely those parts of the slide plates which, when the slide is in its closing position, cover the pivoting arms 67 and 68 together with the side walls 99 and 100. The latching means also include two projections 130 and 131 on either side of the cassette cover 66, which engage corrsponding notches in the walls 99 and 100 of the slide 98.
As is clearly shown especially in FIG. 7 and also in FIG. 9 the cassette cover 66 leaves the front edges 132 and 133 of the side walls 99 and 100 of the slide 98, which are remote from the rear 62 of the cassette housing, free at locations which are disposed nearer the main walls 54 and 55 of the cassette housing. This has been done to provide an abutment for moving the slide 98 to its retracted position when the magnetic tape cassette is placed in a cassette holder of a cassette apparatus, as shown in FIGS. 29 and 30. These figures show a part of a cassette apparatus 134 in cross-section at the location of a cassette holder 135. The cassette holder is pivotable about a hinge pin 136 and is thus movable from a cassette insertion position shown in FIG. 29 to an operating position shown in FIG. 30.
At its front the cassette holder 135 has a cassette insertion opening. By means of tension springs 139 levers 138 urge a cassette against a partly open bottom plate 140, which is provided with upward projections 141 at each side. During insertion of a cassette these projections engage the front edges 132 and 133 of the slide 98. When the cassette 47 is inserted into the cassette holder 135 the slide 98 is thus readily moved from its closing position to its more retracted position.
The side walls 99 and 100 of the slide 98 have notches 142 and 143 which can receive the lateral projections 130 and 131 of the cassette cover in the closed position. As described above, these projections and notches latch the cassette cover in its closed position. However, the projections also enable simple opening of the cassette cover after the cassette has been inserted into a cassette holder of a cassette apparatus. For this purpose a cassette apparatus 134 may include a cover opener 144 which is mounted to the deck of a cassette apparatus 134 by a pin 146 slidable in a slotted hole 147 against upward force of a spring 145. In FIG. 29 the slide 98 already occupies its more retracted position, so that the cassette cover 66 can be pivoted. The cassette cover is pivoted when the cassette holder 135 is moved downwards, during which movement the top of the cover opener 144 engages the projection 130 on the cassette cover 66. The opposite projection 131 can similarly be engaged by a symmetrically located cover opener.
FIG. 26 is similar to FIG. 8 except that the side wall 100 of the slide 98 is now moved towards the more retracted position, while the side wall 99 is still in a position corresponding to the closing position of the slide. In such a situation the slide 98 can readily become jammed on the cassette housing. In order to prevent such an undesired situation the side walls 60 and 61, at the location of the side walls 99 and 100 of the slide 98 when they are in their more retracted positions, have been given a curved profile P with a radius of curvature R which is substantially equal to the distance between the two side walls 60 and 61 of the cassette housing. Thus, at least a limited twisting of the position of the slide 98 relative to the cassette housing is possible without the slide becoming jammed on the cassette housing. For the sake of simplicity FIG. 26 only shows a single radius R, i.e. of the profile P of the side wall 60.
Another embodiment which prevents jamming of the slide is shown in FIGS. 27 and 28. These figures show a magnetic tape cassette 148 which is substantially identical to the magnetic tape cassette shown in FIGS. 6 to 12, except for a slightly different shape of the slide member and

In the cassette 47 the slide 98 and the cassette housing are provided with cooperating stop means to prevent a slide, once mounted, from sliding off the cassette housing, when the cassette cover 66 has not yet been mounted or has been removed. The slide has two inwardly facing bosses 162 and 163 (see FIGS. 12, 16 and 17), and the side walls 60 and 61 of the housing have grooves 164 in which the bosses may move (only one groove shown, in FIGS. 9 and 12). As shown in FIG. 12, the end 165 of the groove 164 serves as a stop for the boss 162. The side wall 61 has a similar groove and end stop for the boss 163. These ends are located so that the bosses abut the respective ends in the closing position of the slide 98. As a result, in the closing position the pressure of the spring 110 is transmitted to the side walls 60 and 61 of the cassette housing by the bosses 162 and 163. The cassette cover 66 and, in particular, the bearing journals 75 to 79 are not loaded by the pressure spring 110 in the closing position of the slide 98, because there is always some clearance between the cassette cover 66 and the slide 98 in its closing position.
Alternative Spring Restraint
FIGS. 24 and 25 schematically show a part of a magnetic tape cassette which is largely identical to the magnetic tape cassette in accordance with FIGS. 6 to 12, but which includes resilient means for loading the cassette cover and the slide member relative to eac

In the situation shown in FIG. 24 the cassette cover 166 is in the closed position and the slide 169 is in the closing position. The slide 169 is pulled towards the cassette cover 166 by the tension spring 172, the assembly being in a stable balanced position. Similarly, in the situation of FIG. 25, in which the cassette cover 166 is in one of its open positions and the slide 169 has been moved into its more retracted position, the cassette cover 166 is in a stable position under the influence of the force exerted on it. The connecting line between the pins 177 and 171 extends on such a side of the bearing journal 173 that the cassette cover tends to swing open further. However, this is prevented by abutment of the bearing journal 174 with the end of its guide slot 178. By suitably dimensioning the spring 172, allowance being made for the weight of the cassette cover 166, the cassette cover is in a stable balanced position for any orientation of the cassette relative to the force of gravity.
PHILIPS VR2022S VIDEO2000 Recording and/or reproducing apparatus:
A magnetic ta
pe recording and/or reproducing apparatus suitable for cooperation with a magnetic tape (1) accommodated in a cassette (10) is provided with a tape guide device (18) which comprises two substantially cylindrical tape guides (19, 20) each mounted on one of two movable supports (21, 22) for withdrawing a portion of the tube from the cassette and wrapping it around a tape guide drum (2). For moving the two supports there is provided a wire drive arrangement (38) which comprises two alternately rotatable wire drums (39, 40) and three wires (41, 42, 43), the first wire (41) passing from the first write drum (39) to the first support (21), the second wire (42) passing from the first support to the second support (22) and the third wire (43) passing from the second support to the second wire drum (40). For simultaneously moving the two supports from their rest positions to their operating positions the first wire drum (39) can be driven and for simultaneously moving the supports from their operating positions to their rest positions the second wire drum (40) can be driven. (FIG. 1).
2. An apparatus as claimed in claim 1, characterized in that each of the two supports takes the form of a sliding member and is movably guided along a guide between its rest position and its operating position, and in that the wire which acts on the first support passes along the guide for the first support and the wire which acts on the second support passes along the guide for the second support.
3. An apparatus as claimed in claim 1, characterized in that the second wire in its path between the two supports is divided so as to for
4. An apparatus as claimed in any of the preceding claims 1, 2, or 3, characterized in that the two wire drums are journalled in the apparatus so as to be coaxial with each other and are rotatable relative to each other, in that the first wire and the third wire each run onto an associated one of the two wire drums and is connected thereto, one of these two wires running onto the associated wire drum in the clockwise direction and the other in the counterclockwise direction, in that for winding in the wires connected to the two wire drums said drums can be driven in opposite directions of rotation, and in that there is provided a spring which acts between the two wire drums and urges the two wire drums relative to each other in opposite directions of rotation.
5. An apparatus as claimed in claim 4, characterized in that the spring takes the form of a flat spiral spring which is substantially coaxial with the wire drums.
6. An apparatus as claimed in claims 4, characterized in that for driving the two coaxial wire drums there is provided a common motor drive arrangement whose direction of rotation is reversible.
8. An apparatus as claimed in claim 7, characterized in that each of the two unidirectional coupling devices comprises a driving projection which projects from the drive member, a coupling projection which projects from a disc which is rigidly connected to the respective wire drum, and a coupling disc which is coaxial with the drive member and which is journalled so as to be rotatable relative to said drive member and the wire drums, which coupling disc comprises a coupling projection for coupling said driving projection to the coupling projection on the disc which is rigidly connected to the respective wire drum.
9. An apparatus as claimed in claim 7, characterized in that for the synchronous motor there is provided a control circuit, which comprises a manually-actuated first switching device which can be switched between two switching positions, for connecting the synchronous motor to an a.c. supply voltage, in one of which switching positions the synchronous motor rotates in a first direction for driving the first wire drum so as to move the supports from their rest positions to their operating positions, and in the other of which switching positions the synchronous motor rotates in a second direction, which is opposite to the first direction, for driving the second wire drum, so as to move the supports from their operating positions to their rest positions, the control circuit further comprising a second switching device which can be actuated when the supports are in their operating positions, which device disconnects the synchronous motor from the a.c. supply voltage and connects it to a d.c. holding voltage when the supports are in their operating positions.
10. An apparatus as claimed in claim 9, characterized in that for positioning the two tape guides when the supports are in their operating positions there is provided on
11. An apparatus as claimed in claim 1, characterized in that for positioning the two tape guides when the supports are in their operating positions there is provided one positioning device for each tape guide and when the supports are in their operating positions the tape guides are each urged into the respective positioning device by means of a separate pressure device which is movable against the action of a return spring from a disengaged position to an engaged position, in that for moving each pressure device to its engaged position a wire guide roller is rotatably journalled on each pressure device, in that the first wire passes round each wire guide roller so as to urge the respective pressure device in the direction of its engaged position, and in that for each pressure device there is provided a separate disengagable latching device which prevents the pressure device from moving to its engaged position when the respective support is out of its operating position and which is disengaged when the respective support is in its operating position.
13. An apparatus as claimed in claim 1, characterized in that the wires are coupled to the supports by detachable coupling means.
14. An apparatus as claimed in claim 13, characterized in that for freely positioning each tape guide when the associated support is in its operating position the detachable coupling means between each wire and the respective support has some lost motion relative to the support.
In this known apparatus the supports for the tape guides take the form of levers which are pivotably journalled in the apparatus, one of two wires, which can jointly be wound onto a single rotatable wire drum, each time acting on said levers for moving said levers from their rest positions to their operating positions, and each time one return spring, which takes the form of an expander spring, acting on said levers for moving them from their operating positions back to their rest positions. When the wire drum is driven the two wires are wound onto said drum, the levers being pivoted against the action of the return springs. Since in this known apparatus the wires are jointly wound onto a single wire drum, it is not unlikely that the wires interfere with each other adversely, which may result in a non-uniform movement of the two supports and thus of the tape guides. This may result in the tape-like record carrier being subjected to a non-uniform load when it is withdrawn from the cassette. In the known apparatus the wires should be adapted to each other accurately in respect of their lengths in order to ensure that the two supports reach their operating positions at the same time. The use of return springs makes it necessary that when the wires are wound up in order to move the supports to their operating positions the drive means for the wire drum has to overcome the return force of the return springs, which demands an extra effort. The two return springs may exert different return forces, which again may result in the two supports being subjected to a non-uniform load. If return springs are employed, steps must be taken to ensure that said springs do not cause an abrupt return of the supports to their rest positions, because in the case of such an abrupt or jerky movement of the supports and the tape guides arranged thereon a correct return of the record carrier is not guaranteed.
It is the object of the invention to provide a recording and/or reproducing apparatus of the type mentioned in the preamble, which mitigates the said pr
In order to move the supports, which are essentially arranged in the apparatus so as to be movable independently of each other but which are functionally coupled to each other by the second wire, from their rest positions to their operating positions the first wire drum is driven and the first wire is wound onto this drum, the third wire being unwound from the second wire drum, which can then rotate substantially without being braked, so that this unwinding is effected practically without any counteraction. In order to move the supports from their operating positions to their rest positions, the second wire drum is driven in a reverse sense and the third wire is wound onto said drum, the first wire being unwound from the first wire drum, which can then also rotate substantially without being braked, so that this unwinding is also effected practically without any counteraction. Thus, for driving each of the two wire drums only one power source is required, which provides only the power necessary for moving the supports and for overcoming the friction effects, the movement of the supports being in no way effected against external return forces. Therefore, the desired result can be obtained with comparatively moderately dimensioned drive means for the wire drums, which in view of low costs and a low power consumption is to be regarded as an advantage.
The fact that the supports, which are functionally coupled to each other by means of a wire, are not only positively driven jointly into their operating positions by driving the first wire drum, but also positively driven into their rest positions by driving the second wire drum, furthermore has the advantage that it is always ensured that the two supports occupy their operating positions in the first-mentioned case and their rest positions in the second case. This arrangement allows accurate switching of any switches that have to be operated at the instant at which the supports reach their rest positions. Thus a switch may be operated to switch off the drive of the second wire drum.
As is known from the said Japanese Patent Application Publication No. 29.705/1978, the two supports may simply take the form of levers, which are pivotably journalled on a spindle which is rigidly mounted on the apparatus. However, it is found to be advantageous if each of the two supports takes the form of a sliding member and
If the path lengths of the two supports between their rest positions and their operating positions are equal, the first, the second and the third wire are each moved over the same wire length when the two supports are moved. For certain reasons of design, for example, due to limited space being available, it may be necessary that the travels of the two supports should be different. In that case the second wire in its path between the two supports may be divided so as to form two separate wire sections, a pair of rotatable transmission drums being provided at the location of this division, which pair comprises two transmission drums of different diameter which are coaxial with each other and are connected to each other, the two wire sections each running onto an associated one of the two trans
Between their connected ends, the wires may be guided by means of wire guides which, for example may take the form of rollers with circumferential grooves for engagement with the wires. In order to ensure that always a satisfactory guidance of the wires is obtained, the wires should always be sufficiently tensioned. In this respect it is found to be advantageous if the two wire drums are journalled in the apparatus so as to be coaxial with each other and are rotatable relative to each other, if the first wire and the third wire each run onto an arronated one of the two wire drums and is connected thereto, one of there two wires onto the associated wire drum in the clockwise direction and the other in the counterclockwise direction, if for winding in the wires connected to the two wire drums, said drums can be driven in opposite directions of rotation, and if there is provided a spring which acts between the two wire drums and urges the two wire drums relative to each other in opposite directions of rotation. Thus it may be ensured by means of the spring that between the wire drum a force is sustained of a magnitude such that the wires between the two wire drums are kept sufficiently taut. The spring may take the form of a flat spiral spring which is substantially coaxial with the wire drums. This provides a simple and compact construction, and such a spiral spring may have a flat spring characteristic so that comparatively large relative movements of the two wire drums are permitted, without the force exerted on the two wire drums by the spring increasing excessively.
The two wire drums may be driven by a common motor drive arrangement whose direction of rotation is reversible. This yields a low-cost and compact embodiment.
The drive means may comprise a d.c. motor. However, the drive arrangement may advantageously comprise a synchronous motor whose direction of rotation is reversible
For the unidirectional coupling devices it is for example, possible to use so-called freewheel mechanisms. However, it is found to be advantageous if each of the two unidirectional coupling devices comprises a driving projection which projects from the drive member, a coupling projection which projects from a disc which is rigidly connected to the respective wire drum, and a coupling disc which is coaxial with the drive member and which is journalled so as to be rotatable relative to said drive member and the wire drums, which coupling disc comprises a coupling projection for coupling said driving projection to the coupling projection on the disc which is rigidly connected to the respective wire drum. Such a coupling device is of a very simple construction and may operate in a troublefree and reliable manner.
For a simple control of the synchronous motor a control circuit may be provided, which comprises a manually-actuated first switching device which can be switched between two switching positions for connecting the synchronous motor to an a.c. supply voltage, in one of which switching positions the synchronous motor rotates in a first direction for driving the first wire drum so as to move the supports from their rest positions to their operating positions and in the other of which switching positions the synchronous motor rotates in a second direction, which is opposite to the first direction, for driving the second wire drum so as to move the supports from their operating positions to their rest positions, the control circuit further comprising a second switching device which can be actuated when the supports are in their operating positions, which device disconnects the synchronous motor from the a.c.
If the two supports are in their operating positions, the two tape guides arranged on the supports are also in their operating positions. To achieve an exact tape path it is essential that the tape guides then occupy an accurately defined position. For positioning the two tape guides when the supports are in their operating positions there may be provided one positioning device for each tape guide and when the supports are in their operating positions the tape guide may each be urged into the respective positioning device by means of a separate pressure device which is movable against the action of a return spring from a disengaged position to an engaged position, and for moving each pressure device to its engaged position a wire guide roller may be rotatably journalled on each pressure device, the first wire passing round each wire guide roller so as to urge the respective pressure device in the direction of its engaged position, and for each pressure device there may be provided a separate disengagable latching device which prevents the pressure device from moving to its engaged position when the respective support is out of its operating position and which is disengaged when the respective support is in its operating position. In this way the wire drive arrangement provided for moving the support may also be used for moving the pressure devices, so that a separate drive arrangement for the pressure devices may be dispensed with.
For a simple construction the two pressure devices may each comprise a pressure slide, the two slides being movable parallel to each other, and on each slide an essentially U-shaped pressure member being pivotably journalled for cooperation with the respective tape guide, there being provided a single disengagable latching device which is common to the two pressure devices and acts between the two pressure slides. In this way a compact arrangement may be obtained.
One of the two pressure devices may comprise a switching lever which is pivotably journalled on said device, which lever under the influence of a retaining spring is retained against a stop on said one of the pressure devices, and on which lever the wire guide roller on said one of the pressure devices is rotatably journalled, the switching lever, when said one of the pressure devices is in its engaged position, being kept in a switching position by cooperation between the first wire and said wire guide roller, in which position the switching lever is disengaged from the stop against the action of the retaining spring and the switching lever being coupled to the second switching device of the control circuit for the synchronous motor, which when the switching lever is in its switching position ensures that the synchronous motor remains connected to its d.c. holding voltage. In this way it is ensured that the synchronous motor, which is connected to the d.c. holding voltage and which is thus held stationary, not only keeps the supports in their operating positions but also keeps the pressure devices in their engaged positions, so that separate retaining devices for retaining the pressure devices in their engaged positions may be dispensed wi
The connections between the supports and the wires may, for example, be established by permanent clamping connections. However, it is found to be advantageous to provide detachable couplings. In this way it may be ensured that the supports can be mounted in a simple manner and may be removed, for example, for the purpose of cleaning. For the detachable coupling a pin-and-slot-connection may be used. This pin-and-slot-connection may, for example, comprise a lug which is attached to the wire and a pin which projects from the support and which engages with the lug. Alternatively, a coupling element may be rigidly connected to the wire and the support may be formed with a coupling recess, in which the coupling element engages.
The invention will be described in more detail with reference to the drawings, which show two embodiments to which the invention is not limited. In the drawings:
FIG. 1 is a schematic plan view showing the parts which are relevant to the invention, of a recording and/or reproducing apparatus for a record carrier in the form of a tape which is accommodated in a cassette, which apparatus for wrapping the record carrier around a tape guide drum comprises two tape guide pins each arranged on a support in the form of a sliding member, the two sliding members, which are movable between a rest position and an operating position by means of a wire drive arrangement being shown in their rest position.
FIG. 2 shows the apparatus of FIG. 1 with the sliding members in their operating positions,
FIG. 3 is a cross-section through one of the two sliding members in its operating position, taken on the line III--III in FIG. 2,
FIG. 4 is a cross-section through a detail of the apparatus in accordance with FIGS. 1 and 2 taken on the line IV--IV in FIG. 1,
FIG. 5 is a cross-section through a detail of the apparatus of FIGS. 1 and 2 on the line V--V in FIG. 1,
FIG. 6 is a cross-section through a detail of the apparatus of FIGS. 1 and 2 taken on the line VI--VI in FIG. 1,
FIG. 7 shows the same detail as FIG. 6 in a cross-section taken on the line VII--VII in FIG. 2.
FIG. 8 represents a control circuit for a synchronous motor employed in the apparatus of FIGS. 1 and 2,
FIG. 9 is a schematic plan view showing the parts which are relevant for the invention, of an other recording and/or reproducing apparatus, in which the tape guides take the form of rollers and the supports for the tape guide rollers take the form of pivotable levers, which are shown in their rest positions, and
FIG. 10 shows the apparatus of FIG. 9 with the levers in their operating positions.
FIGS. 1 and 2 schematically represen
ts a recording and/or reproducin

The apparatus furthermore comprises a stationary magnetic head 7, by means of which a track which extends along the tape 1 in the longitudinal direction thereof can be scanned and an audio signal associated with the television signal can be recorded or reproduced. In addition to the magnetic head 7 there is provided a further stationary magnetic head 8, by means of which the same track can be scanned as is scanned by the magnetic head 7 and which is adapted to erase audio signals recorded in this track. A further stationary magnetic head 9 has been provided for simultaneously erasing the television signals recorded in the oblique tracks and the associated audio signal recorded in a longitudinal track.
As can be seen in FIG. 1, the tape 1 is accommodated in a rectangular cassette 10 which can be supported on the apparatus, which cassette comprises
In order to withdraw the tape from the cassette 10 and wrap it around the tape guide drum 2, and at the same time bring the tape into operative contact with the magnetic heads 7, 8 and 9 and with the capstan 5, the apparatus is provided with a tape guide device 18, which comprises two substantially cylindrical tape guides 19 and 20 in the form of pins. It is obvious that the tape guides may alternatively take the form of rollers. The tape guide pins 19 and 20 are each arranged on one of two movable supports 21 and 22 in the apparatus. The supports 21 and 22 are movable between a rest position, shown in FIG. 1, in which the tape guide pins 19 and 20 are located inside the trough-shaped recesses 17 in the major walls of the cassette 10 and engage behind the tape 1 accommodated in the cassette at the location of the opening 16 in said cassette, and an operating position, shown in FIG. 2, in which the tape guide pins 19 and 20 keep the tape, which is pulled out of the cassette by the pins when the supports are moved from their rest positions to their operating positions, wrapped around the tape guide drum 2.

For moving the two sliding members 21 and 22 between their rest positions and their operating positions there is provided a wire drive arrangement 38. The wire drive arrangement comprises two rotatable wire drums 39 and 40 and two wires 41 and 42 which each act on one of the two sliding members substantially in the direction of movement of the sliding member 21 or 22 from its rest position to its operating position. The wire 41, which acts on the first sliding member 21 substantially in the direction of movement of said member from its rest position to its operating position, passes to the first wire drum 39. The second wire 42, which acts on the second sliding member 22 essentially in the direction of movement of said member from its rest position to its operating position, passes to the first sliding member 21 and acts on this sliding member substantially in the direction of movement of said member from its operating position to its rest position, so th
The first wire 41 passes from the first drum 39 via a first wire guide roller 44, a second wire guide roller 45, a third wire guide roller 46 and a fourth wire guide roller 47 to the guide 23 for the first sliding member 21 and, as stated previously along this guide to the first sliding member 21. The second wire 42 passes from the first sliding member 21, along the guide 23 for the first sliding member 21, as stated previously, to a fifth wire guide roller 48 and thence via a sixth wire guide roller 49 to a pair of rotatable transmission drums 50. From the pair of transmission drums 50 the second wire passes via a seventh wire guide roller 51 to the guide 24 for the second sliding member 22 and, as stated previously, along this guide to the second sliding member 22. The third wire passes from the second sliding member 22, as stated previously, along the guide 24 for the second sliding member 22 to an eighth wire guide roller 52 and thence via a ninth wire guide roller 53 to the second wire drum 40.
The second wire 42 extends between the two sliding members 21 and 22 so that two separate wire sections 54 and 55 are formed. At the location where the second wire 42 is divided the pair of transmission drums 50 is arranged, which is shown in more detail in FIG. 5.
The pair of transmission drums 50 comprises two drums 57 and 58 which are coaxial with each other, which are rotatable about a fixed spindle 56 in the apparatus, and which are rigidly coupled to each other, said drums having different diameters. The two wire sections 54 and 55 run in opposite directions onto the two drums 57 and 58 respectively and are connected to the respective drums. In the present case the wire section 54 runs onto the drum 57 in the anti-clockwise direction (as viewed in FIGS. 1 and 2) and the wire section 55 runs onto the drum 58 in the clockwise direction. Thus the wire section 54, which acts on the first sliding member 21 which has a greater travel, is connected to the drum having the greater diameter and the wire section 55, which acts on the second sliding member 22 which has a smaller travel, is connected to the drum 58 having the smaller diameter. When the sliding members are moved the drum 57 takes up or pays out a greater wire length than is paid out or taken up by the drum 58. The diameters of the two drums have been selected so that the difference between the wire length wound on one drum and the wire length which is simultaneously unwound from the other drum exactly corresponds to the difference in travel of the two sliding members between their rest positions and operating positions, thus simply compensating in a simple manner for the different travels of the two sliding members, which are coupled to each other by means of the second wire.
It is to be noted that in the present case the first wire 41 and the wire section 54 belong to a continuous length of wire, which passes from the first wire drum 39 to the drum 57 of the pair of transmission drums 50 and which acts on the first sliding member 21, and that the wire section 55 and the third wire 43 belong to a further continuous length of wire, which passes from the drum 58 of the pair of transmission drums 50 to the second wire drum 40 and which acts on the second sliding member 22. Obviously, the first wire 41, the second wire 42 and the third wire 43 may all belong to a single continuous length of wire. If required, it is also possible that the first wire 41, the second wire 42 and the third wire 43 may be formed by separate lengths of wire.
The wires 41, 42, 43 act on the supports formed by the sliding members 21 and 22, as can be seen in FIGS. 1, 2 and 3, via d

For moving the two sliding members 21 and 22 from their rest positions to their operating positions, the first wire drum 39 can be driven in a clockwise direction (as viewed in FIGS. 1 and 2) and for moving the two sliding members from their operating positions to the rest positions the second wire drum 40 can be driven in an anti-clockwise direction. When the first wire drum 39 is driven the first wire 41 is wound onto said drum, the first sliding member 21 being pulled from its rest position to its operating position by the first wire 41 which acts on said member. The second sliding member 22, which is coupled to the first sliding member 21 via the second wire 42, is then also pulled from its rest position to its operating position, the third wire 43, which acts on the second sliding member 22, then being unwound from the second wire drum 40. When the second wire drum 40 is driven, the process is reversed, the two sliding members 21 and 22 being jointly pulled from their operating positions into their rest positions.
As can be seen from FIGS. 1, 2 and 4, the two wire drums 39 and 40 are journalled in the apparatus coaxially with each other and are rotatable relative to each other. For this purpose a sleeve 66 is slid onto a spindle 65 which is rigidly mounted in the apparatus. The first wire drum 39 is rotatable around the sleeve 66 while the second wire drum 40 is rigidly connected to the sleeve. The first wire 41 and the third wire 43 run in opposite directions onto the two wire drums 39 and 40 respectively, i.e. the first wire 41 runs onto the first wire drum 39 in a clockwise direction (as viewed in FIGS. 1 and 2) and is connected thereto and the third wire 43 runs onto the second wire drum 40 in an anti-cloc

The two drums 39 and 40 also have different diameters, the first wire drum 39, onto which the first wire 41 runs, having a greater diameter than the second wire drum 40, onto which the third wire 43 runs. The diameters have been selected in conformity with the different travels of the two sliding members, so that although different lengths of the first wire 41 and the third wire 43 are wound in and paid out by the respective drums, because of the different travels of the two sliding members 21 and 22, no relative movement occurs between the two wire drums during the movement of the sliding members. Thus, when the two sliding members are moved, the force of the spring 67 acting between the two wire drums will not change, so that the influence of the spring on the wire drums and thus on the wires extending between the two wire drums will neither vary during the movement of the sliding members.
Each of the two unidirectional coupling devices 76 and 77 respectively comprises a driving projection 78 and 79 respectively, which projects axially from the gear wheel 75, eccentrically thereof a coupling projection 82 and 83 respectively, which projects axially from a disc 80 and 81 respectively eccentrically thereof, which discs are rigidly connected to the respective wire drums 39 and 40, and a coupling disc 84 and 85 respectively, which is coaxial with the gear wheel 75 and is rotatable around the sleeve 66 and relative to the gear wheel 75 and the wire drums. Each of the two coupling discs 84 and 85 is provided with a radially projecting coupling projection 86 and 87 respectively, for coupling the driving projection 78 and 79 respectively to the coupling projection 82 and 83 respectively. In the present case the disc 80, which is rigidly connected to the first wire drum 39, from which disc the coupling projection 82 projects, is constituted directly by a flange on the wire drum. The disc 81, which comprises the couplin
For controlling the synchronous motor 72 there is provided a control circuit 89 which is shown in FIG. 8. In order to start the movements of the sliding members 21 and 22 from their rest positions to their operating positions the apparatus comprises a manually actuated button 90, which is automatically locked in its on-position and upon whose actuation a switch 91 is closed which is included in the circuit of an electromagnet 92 which is connected to a d.c. supply voltage V, so that when the button 90 is actuated the magnet 92 is energized. In order to start the movements of the sliding members from their operating positions to their rest positions, the apparatus also comprises a manually-actuated button 93, which is automatically locked in its on-position and upon whose actuation the switch 91 is opened, so that when the button 93 is actuated the magnet 92 is not energized. The two buttons 90 and 93 are constructed so that upon actuation of one of the two buttons the other button, if actuated, is released from its on-position, as is symbolically indicated by the broken line 94.
FIG. 8 shows diagrammatically two exciter coils 93 and 94 of the synchronous motor 72, which coils at one end are directly connected to each other and as the other end are connected to each other via a phase-shifting capacitor 95. The rotor, not shown, in this case comprises a permanent magnet with a predetermined member of poles. For driving the synchronous motor an a.c. supply voltage can be applied between terminal 96 and, depending on the desired direction of rotation of the synchronous motor 72, one of the two terminals 97 and 98 of the synchronous motor, the a.c. supply voltage being applied to the other of th
When the electromagnet 92 is energized by actuation of the button 90, the first switching device 103 is set to the switching position represented by a broken line in FIG. 8,
in which the synchronous motor 72 is connected to the a.c. supply voltage with its terminal 97 via the first switching device 103 and, for driving the first wire drum 39 in order to move the sliding members 21 and 22 from their rest positions to their operating positions, rotates in a first direction of rotation, namely in the present case in an anti-clockwise direction (as viewed in FIGS. 1 and 2). If the electromagnet 92 is de-energized by actuation of the button 93, the first switching device 103 is set to the switching position represented by a solid line in FIG. 8, in which the synchronous motor is connected to the a.c. supply voltage with its terminal 98 via the first switching device 103 and for driving the second wire drum 40 in order to move the sliding members from their operating positions to their rest positions, rotates in a direction of rotation opposite to the first direction of rotation, i.e. in the present case in a clockwise direction.
As can be seen in FIG. 8, the secondary winding 99 of the transformer 100 has a tapping 106, which is connected to a rectifier circuit 109, which comprises a diode 107 and a charging capacitor 108, for rectifying the alternating voltage appearing on the tapping 106. In this way a d.c. holding voltage for the synchronous motor 72 is obtained on the terminals 110 and 111 of the charging capacitor 108, by means of which as soon as it is applied to the synchronous motor said motor is braked. The terminal 111 of the charging capacitor 108 is connected directly to the terminal 96 of the synchronous motor 72. For applying the d.c. holding voltage to the synchronous motor, the control circuit 89 comprises a second switching device 112 in the form of a simple change-over switch, whose main co
The control circuit 89 furthermore comprises a switch 116, which is included in the connection between the second contact 105 of the first switching device 103 and the terminal 98 of the synchronous motor. Via this connection the synchronous motor 72 can receive the a.c. supply voltage for driving said motor in a clockwise direction, so as to move the sliding members from their operating positions to their rest positions. The switch 116 can then be actuated only when the sliding members 21 and 22 are in their rest positions. In the present case the switch 116, as can be seen in F

Furthermore, the control circuit 89 comprises a switch 117, which in a similar way to the first switching device 103 can be actuated by the electromagnet 92 and is included in the connection between the first contact 114 of the second switching device 112 and the terminal 110 of the charging capacitor 108. If the electromagnet 92 is energized upon actuation of the button 90, in order to move the sliding members from their rest positions to their operating positions, the switch 117 is in its closed switching position represented by a broken line in FIG. 8. Thus, when the sliding members are in their operating positions, the second switching device 112 being in the switch position which is also represented by a broken line in FIG. 8, the d.c. holding voltage can be applied to the synchronous motor 72 via the switch 117 and the second switching device 112, so that the synchronous motor is then braked. If the electromagnet 92 is de-energized by actuating the button 93 in order to start the movement of the sliding members from their operating positions to their rest positions, the switch 117 is in its open switch position represented by a full line in FIG. 8, so that the d.c. holding voltage is then no longer applied to the synchronous motor 72 and consequently the synchronous motor is no longer braked.
Each pressure device 129 and 130 comprises a pressure slide 131 and 132 respectively, the two pressure slides being arranged in the apparatus so as to be movable parallel to each other in a manner not shown. The return spring 128, which tends to keep the two pressure devices in their disengaged positions, simply acts directly on each of the two pressure slides 131 and 132 in a corresponding manner. The disengaged positions of the two pressure devices, which are shown in FIGS. 1 and 6, are defined by two fixed stops 133 and 134 on the apparatus for the pressure slides 131 and 132, the pressure slide 131 being held in the disengaged position against the stop 133 under the influence of the return spring 128 and the pressure slide 132 being held in the disengaged position of the pressure device 130 against the stop 134 under the influence of the return spring 128. The engaged positions of the two pressure devices, which are shown in FIGS. 2 and 7, are automatically obtained when the pressure devices press the tape guide pins into the positioning devices.
The pressure slide 131 comprises an L-shaped bearing-bracket 135, on which an essentially U-shaped pressure member 136 is journalled to pivot about an axis 137, which pressure member, when
The pressure slide 132 also comprises an essentially U-shaped pressure member 143, which is pivotable about an axis 142 and which with its limbs 144 and 145 is adapted to press the tape guide pin 20 into the positioning groove 127 of the positioning device 119 when the sliding member 22 is in its operating position. The pressure member 143 comprises an L-shaped finger 146, whose hooked free end projects into an aperture 147 in the pressure slide 132, so that the pivoting range of the pressure member 132 is effectively limited.
In the present case the pressure device 130 comprises a switching lever 149 which is journalled on the pressure slide 132 of said device to pivot about an axis 148. The switching lever 149 has a beat and portion 151 which abuts a stop face 152 on the pressure slide 132 of the pressure device 130 under the influence of a retaining spring 150, which takes the form of a tension spring and acts between the pressure slide 132 and the switching lever 149.
For setting each of the two pressure devices 129 and 130 to their engaged positions against the action of the return spring 128 a wire guide roller is rotatably journalled on each pressure slide 131 and 132 and the first wire 41 passes round each of these two wire guide rollers and urges the pressure devices towards their engaged positions, that is to say, when the first wire drum 39 is driven the first wire 41 tends to set the pressure devices 129 and 130 from their disengaged positions to their engaged positions. The said wire guide rollers are the two wire guide rollers 45 and 46, the wire guide roller 45 being rotatably journalle
The pressure devices 129 and 130 should not be moved from their disengaged positions to their engaged positions until the sliding members 21 and 22 are in their operating positions, because only then can the tape guide pins 19 and 20 be urged into the positioning grooves 126 and 127 by the pressure members 136 and 143. For this reason there is provided a disengageable latching device 153 which prevents a movement of each pressure device 129 and 130 to its engaged position when the sliding member is not in its operating position and which is disengaged when the sliding member is in its operating position. In the present case there is provided a single disengagable latching device 153 which is common to the two pressure devices 129 and 130 and which acts between the two pressure slides 131 and 132.
The latching device 153 comprises a leaf spring 154 which is secured at one end to the pressure slide 131 and whose free end 155 is bent through two right angles in opposite directions to form a shoulder 155 on the spring. This shoulder cooperates with a stop face 156 formed on the pressure slide 132, that is to say, in the non-released position of the latching device 153 the stop face 156 is held against the shoulder 155 of the leaf spring 154 by the tensile action of the wire 41 which passes around the wire guide rollers 45 and 46 and which is kept taut by the tension spring 67 which acts between the two wire drums 39 and 40, as stated previously.
Thus, in addition to the supports which take the form of sliding members, the pressure devices also can be actuated by means of the wire drive arrangement, so that a separate drive for the pressure devices may be dispensed with. The provision of only one disengagable latching device for the two pressure devices results in a simple, cheap and compact construction. The connection of the synchronous motor to its d.c. holding voltage via a switching lever mounted on a pressure device has the advantage that the motor which is thus braked not only keeps the supports in their operating positions but also keeps the pressure devices in their engaged positions, so that separate retaining devices for retaining the pressure devices in their engaged positions may be di
The operation of the apparatus described in the foregoing will now be explained in more detail. For moving the sliding members 21 and 22 from their rest positions to their operating positions the button 19 is actuated, so that the electromagnet 92 is energized and thus the a.c. supply voltage is applied to the synchronous motor in such a way that said motor is driven in the anti-clockwise direction. The gear wheel 75 is thereby rotated in the clockwise direction and via the driving projection 78, the coupling projection 86 of the coupling disc 84 and the coupling projection 82, the first wire drum 39 is driven in a clockwise direction, the second wire drum 40 also being driven via the spring 67. As a result of this the first wire 41 is wound onto the first wire drum 39 and consequently the first sliding member 21, on which via the coupling attachment 61 the first wire acts substantially in the direction of the movement of the sliding member from its rest position to its operating position, is pulled from its rest position to its operating position along the guide 23, the wire section 54 of the second wire 42, which via the coupling attachment 61 acts on the first sliding member substantially in the direction of movement of said member from its operating position to its rest position, being unwound from the transmission drum 57. At the same time the wire section 55 of the second wire is wound onto the transmission drum 58 and as a result of this the second sliding member 22, which is coupled to the first sliding member 21 via the second wire and on which via the coupling attachment 62 the wire section 55 of the second wire acts substantially in the direction of movement of the sliding member 22 from its rest position to its operating position, is also pulled from its rest position to its operating position along the guide 24, the third wire 43, which via the coupling attachment 62 acts on the second sliding member essentially in the direction of movement of this sliding member from its operating position to its rest position, being unwound from the second wire drum 40, which in this direction of rotation is driven via the spring 67. In this way the two sliding members 21 and 22, which are coupled to each other by the second wire 42, are pulled to their operating positions in a precisely coordinated and uniform manner, the tape guide pins 19 and 20 on the sliding members 21 and 22 pulling the tape 1 out of the cassette 10, wrapping it around the tape guide drum 2 and bringing it into contact with the magnetic heads 7, 8 and 9 and with the capstan shaft 5, from which the pressure roller 6 is at that time, of course disengaged. Obviously the reels in the cassette must be free to rotate. In this respect it is to be noted that the two sliding members, despite their different travels, reach their operating positions simultaneoulsy, because as stated previously the difference in travel has been compensated for with the aid of the transmission drums.
When the sliding members 21 and 22 reach their operating positions the coupling attachm
Therefore, as soon as the pressure devices occupy their engaged positions, said devices cannot be moved any further. However, as the first wire 41 is wound further onto the first wire drum 39, the first wire exerts a tension on the wire guide roller 46 such that the switching lever on which the wire guide roller 46 is mounted is pivoted into its switching position, which is represented by full lines in FIG. 7, against the action of the retaining spring 150. In this switching position the switching lever 149 actuates the second switching device 112 so that the main contact 113 is electrically connected to the first contact 114 of the second switching device. As a result of this the synchronous motor 72 is disconnected from the a.c. drive voltage and connected to the d.c. holding voltage, so that the synchronous motor is braked. Thus, winding of the first wire 41 is discontinued and via the wire drive arrangement 38 the braked synchronous motor keeps the switching lever 149 in its switching position, the pressure devices 129 and 130 in their engaged positions, and the sliding members 21 and 22 for the tape guide pins 19 and 20 in their operating positions.
In this situation it is ensured that the tape guide pins 19 and 20 are retained in the positioning grooves 126 and 127. As can be seen in FIG. 2, the tape 1, which has been withdrawn from the cassette 10, then extends from the reel 11 via the guide roller 13, the tape guide pin 19, the magnetic head 9, the tape guide drum 2, the magnetic head 8, the magnetic head 7, the tape guide pin 20, the capstan 5, a further tape guide pin 161 and the guide roller 15 to the reel 12. If the reels 11 and 12, the capstan 5 and pressure roller 6, the rotatable magnetic heads 3 and 4 in the tape guide drum 2 and the magnetic heads 7, 8 and 9, are then put into operation, television signals and associated audio signals can be recorded on the tape or reproduced therefrom.
In order to return into the cassette the portion of the tape which has been withdrawn therefrom, the sliding member supporting the tape guide
As the synchronous motor is connected to the a.c. supply voltage, as stated previously, said motor will be driven in the clockwise direction. Thus, the gear wheel 75 is driven in the anti-clockwise direction. Via the driving projection 79, the coupling projection 87 of the coupling disc 85 and the coupling projection 83 of the disc 81, which disc via the sleeve 66 is rigidly connected to the second wire drum 40, the rotation of the gear wheel 75 is transmitted to the second wire drum 40, so that this drum is also driven in the anti-clockwise direction. As a result of this the third wire 43 is wound onto the second wire drum 40, so that the second sliding member and the first sliding member, which is coupled to the second sliding member via the second wire, are moved from their operating positions to their rest positions the first wire 41 being unwound from the first wire drum 39. During this operation at least one of the two reels can be driven in the appropriate manner in order to return the tape into cassette, so as to take up the tape which has been withdrawn from the cassette.
As is apparent from the foregoing description, a well-coordinated movement of the tape guide pins is ensured by the joint movement of the supports for the tape guide pins, which supports are arranged so as to be movable in the apparatus independently of each other but are coupled to each other by means of a wire. As only one wire can be wound on each wire drum, this winding can be effected very uniformly, so that the supports with the tape guide pins also move very uniformly and smoothly, which results in a particularly smooth and gentle withdrawal of the tape from the cassette and return of the tape into the cassette.

The recording and/or reproducing apparatus of FIGS. 9 and 10 comprises two leve
rs 162 and 163 as supports for the tape guides, which levers are pivotable between their rest positions and their operating positions about spindles 164 and 165 respectively, which are rigidly mounted in the apparatus. The levers 162 and 163 carry rotatable tape guide rollers 166 and 167 respectively, which function as tape guides. The rest positions of the levers are shown in FIG. 9 and the operating positions in FIG. 10.
For moving the two levers 162 and 163 there is again provided a wire drive arrangement 38, which comprises two rotatable wire drums 39 and 40, which in this case are not arranged coaxially, as in the apparatus shown in FIGS. 1 to 8, but are spaced from each other transversely of their axes. Furthermore, the wire drive arrangement 38 again comprises a first wire 41, a second wire 42, and a third wire 43, the first wire 41 passing from the first wire drum 39, to which it is connected, via a stationary oval first wire guide 168 to the end 169 of the first lever 162 which carries the tape guide roller 166, and acting on said lever substantially in the direction of movement of said lever from its rest position to its operating position. The second wire 42, which acts on the first lever 162 substantially in the direction of movement of said lever from its operating position to its rest position, passes from the end 169 of the first lever 162 via a stationary oval second wire guide 170 and a stationary oval third wire guide 171 to the end 172 of the second lever 163 which carries the tape guide roller 166. The second wire 42 acts on the second lever 163 substantially in the direction of movement of said lever from its rest position to its operating position. The third wire 43, which acts on the second lever 163 substantially in the direction of movement of said lever from its operating position to its rest position, passes from the end 172 of the lever 163 via a stationary oval fourth wire guide 173 to the second wire drum 40 and is connected thereto. The oval wire guides have circumferential grooves in which the wires are guided. In the present case the wires 41, 42 and 43 are constituted by a continuous wire which extends between the two wire drums 39 and 40 and is attached to the levers in a schematically represented manner.
For driving the first motor 174 to move the levers from their rest positions to their operating positions, said motor can be connected to a d.c. supply voltage V via a switch 176. The switch 176 can be closed by the button 90 for starting the movement of the levers from their rest positions to their operating positions. For driving the motor 175 to move the levers from their operating positions to their rest positions, this motor can be connected to the d.c. supply voltage V via a switch 177. The switch 177 can be closed by means of the button 93 for starting the movement of the levers from their operating positions to their rest positions. Again the two buttons, which are automatically retained in their on-positions, are constructed so that when one of the two buttons 90 or 93 is actuated the other button, if actuated, is released, as is symbolically represented by the broken line 94.
For switching off the first motor 174 after the two levers 162 and 163 have been moved from their rest positions to their operating positions, there is provided a switch 178 included in the circuit of the first motor 174, which switch can be actuated in the operating position of the first lever 162 and is closed when the lever 162 is not in its operating position, in which case the motors 174 can be driven, and is open when the lever 162 is in its operating position, in which case the drive of the motor 174 is interrupted. For switching off the second motor 175 after the two levers 162 and 163 have been moved from their operating positions to their rest positions, there is provided a switch 179 which can be actuated by the second lever 163 and which is included in the circuit of the second motor 175, which switch is closed when the lever 163 is not in its rest position, in which case the motor 175 can be driven, and is open when the lever is in its rest position, in which case the drive of the motor 175 is interrupted.
For holding the two wire drums 39 and 40 stationary after each movement of the levers 162 and 163 supporting the tape guide rollers 166 and 167, there is provided a disengagable latching device 180 and 181 for each wire drum. Each of the two latching devices 180 and 181 comprises a pivotable latch 184 and 185 respectively, which is movable by means of an electromagnet 182 and 183 respectively. The two latches are adapted to cooperate with teeth 186 and 187 on the two wire drums 39 and 40 respectively, the latches 184 and 185 engaging the teeth 186 and 187 with their hooked free ends 188 and 189 when the electromagnets 182 and 183 are energized, as shown in full lines in FIGS. 9 and 10, and the free ends of the latches being disengaged from the respective teeth when the electromagnet
The two electromagnets 182 and 183 are each connected to earth with one terminal, the two other terminals being interconnected at a terminal 190. Via the parallel connection of two series-connected switches 191 and 192 and 193 and 194 respectively, the d.c. supply voltage V can be applied to the terminal 190. The two switches 191 and 193, which are open in their rest position, can be actuated by the second lever 163. The switch 191 is closed by the second lever 163 when the lever 163 is in its rest position, the electromagnets 182 and 183 then being energized via the switch 192 and the switch 191, and the latches 184 and 185 being in engagement with the teeth 186 and 187 in order to hold the wire drums 39 and 40. The switch 193 is closed by the second lever 163, if said lever is in its operating position, the electromagnets 182 and 183 then being energized via the switch 194 and the switch 193, and the latches 184 and 185 engaging with the teeth 186 and 187 of the wire drums 39 and 40 in order to hold said drums. The switch 192, which is closed in its rest position, can be actuated by the button 90 in order to start the movements of the levers 162 and 163 from their rest positions to their operating positions, and the switch 194, which is also closed in its rest position, can be actuated by the button 93 in order to start the movements of the levers from their operating positions to their rest positions, each button 90 or 93 opening the switch 192 or 194 respectively which is actuated thereby. Upon actuation of each of the two buttons for starting the movements of the levers 162 and 163 the circuit of the electromagnets 182 and 183 is interrupted, so that the latches 184 and 185 are disengaged from the teeth 186 and 187 and the wire drums 39 and 40 can again be driven by their motors 174 and 175.
To move the levers 162 and 163 from their operating positions shown in FIG. 10 to their rest positions shown in FIG. 9, so as to enable the tape 1 to be returned into the cassette 10, the button 93 is actuated. As a result of this, the switch 194 is opened. Since, as stated previously, the switch 191 is in its open switching position, the d.c. supply voltage V is disconnected from the electromagnets 182 and 183 when the switch 194 is opened, so that the latches 184 and 185 are released to allow the wire drums 39 and 40 to rotate. Moreover, switch 177 is closed as a result of the actuation of the button 93, so that the second motor 175 is connected to the d.c. supply voltage and is thus driven in the clockwise direction. The second motor 175 drives the second wire drum 40 in the clockwise direction also. The third wire 43 is then wound onto the second wire drum 40, said wire 43, which acts on the second lever 163, then moving said lever from its operating positions to its rest position. During this movement the first lever 162, which is coupled to the second lever 163 via the second wire 42, is also moved from its operating position to its rest position, the first wire 41, which acts on the first lever 162, being unwound from the first wire drum 39. The first wire drum 39 then rotates substantially without being braked, because the first motor 174 is not braked. As soon as the two levers 162 and 163 have left their operating positions, the switch 178 is closed and switch 193 is opened. As soon as the two levers 162 and 163 occupy their rest positions, the switch 179 is closed so that the second motor 175 and thus the second wire drum 40 is stopped, and the switch 191 is closed so that the electromagnets 182 and 183 are energized and the wire drums 39 and 40 are held by means of the latches 184 and 185. In this way it is ensured that the levers 162 and 163 are maintained in their rest positions, which are defined by the positions of the switches 179 and 191.
In this embodiment the coupling of the two levers, which are essentially pivotable independently of each other, by means of a wire ensures a precisely coordinated movement of the levers and thus of the tape guide rollers. Since again only one wire is wound on each wire drum, winding can be effected uniformly and smoothly, which results in a very smooth and uniform movement of the tape guide rollers. Thus, the tape is not subjected to non-uniform loads. By providing two separate drive means for the two wire drums, which are spaced from each other transversely of their axes, these drive means may be of very simple construction. Holding the wire drums by means of switchable latches is advantageous, because a comparatively large effort is required only for switching the latches and not for retaining the latches in their engaged positions, in which they are engaged with the wire drums. This is advantageous for a minimal power consumption.
Obviously the invention is not limited to the two embodiments described in the foregoing, because a series of modifications to these embodiments is possible. This is possible in respect of, for example, the construction of the supports and the tape guides arranged on the supports. Furthermore, it is also possible in respect of the drive means for the two wire drums, as well as the means for holding the wire drums stationary after the supports have been moved.
In a helical scan video recorder in which the magnetic heads are arranged on bimorph piezoelectric actuators it may be desirable, in order to counteract depolarization of the piezoelectric elements, to bias these elements. This is possible without the use of additional slip rings if the electrode to which the drive voltage is applied is connected, via a dio
1. An apparatus for recording and/or reproducing information on a record carrier in the form of a tape in tracks which are inclined relative to the longitudinal axis of the record carrier, which apparatus comprises
a first magnetic head,
a first electro-mechanical actuator on which said magnetic head is arranged for controlling the position of said magnetic head in a direction transverse to the tracks, said actuator comprising two piezoelectric transducers which are each arranged on one side of a common electrode and which are each provided with an electrode on the side which is remote from said common electrode,
a rotatable body, on which said actuator is mounted, for moving the magnetic head in the track direction,
a tracking signal generator for supplying a signal to the actuator for controlling the position of the magnetic head relative to the tracks,
a drive signal input which is coupled to electrodes of the piezoelectric transducers in such a way that the transducer deflects as a function of the signal applied to said drive signal input, and
a first rotary signal-coupling means for coupling the drive signal generator to the drive signal input of actuator, characterized by
a bias voltage input for applying a bias voltage so that both piezoelectric elements are biased in the direction of polarization, at least during periods in which they are driven by the drive signal,
a buffer element for buffering said bias voltage during said periods,
a first voltage isolator between the bias voltage input and the drive voltage input, and
2. An apparatus as claimed in claim 1, comprising a second electro-mechanical actuator of the same type as the first actuator, which second actuator carries a second magnetic head, is also mounted on the rotatable body, and is connected to the tracking signal generator via a second rotary signal coupling means and switching means, characterized in that the bias voltage input of said second actuator is connected to the bias voltage input of the first actuator, both bias voltage inputs have a common connection to the buffer element, and a second voltage isolator is arranged between the drive voltage input of the second actuator and the bias voltage input of said second actuator.
3. An apparatus as claimed in claim 1 or 2, characterized in that the buffer element comprises a capacitor.
4. An apparatus as claimed in claim 3, characterized in that the first or the second voltage isolator comprises a diode which is poled in the forward direction between the relevant drive voltage input and the relevant signal voltage input.
5. An apparatus as claimed in claim 4, characterized in that the two piezoelectric elements arranged on both sides of the common electrode are biased in opposite directions relative to said common electrode, the drive voltage input is connected to the other electrode of one piezoelectric element and the other electrode of the other piezoelectric element is coupled to earth.
a first magnetic head,
a rotatable body, on which said actuator is mounted for moving the magnetic head in the track direction,
a tracking-signal generator for applying a signal to the actuator for controlling the position of the magnetic head relative to the tracks,
a drive-signal input which is coupled to electrodes of the piezoelectric transducers in such a way that the transducer deflects as a function of the signal applied to said drive-signal input, and
a first rotary signal-coupling means for coupling the tracking-signal generator to the drive-signal input of the actuator.
a bias-voltage input for applying a bias so that both piezoelectric elements are biased in the direction of polarization, at least during periods in which they are driven by the drive signal,
a buffer element for buffering said bias voltage during said periods,
a first voltage isolator between the bias-voltage input and the drive-voltage input, and
switching means arranged between the tracking-signal generator and the signal-coupling means, for alternately connecting the drive-signal input to the tracking-signal generator and a source of bias voltage via said signal-coupling means.
The invention is based on the recognition of the fact that it is thus possible to apply a voltage pulse, for example at times when the head is not used (for example during the period in which the second head follows the track). This voltage pulse is applied to the buffer via the voltage isolator. If subsequently the drive signal, whose amplitude is lower, is applied the voltage isolator isolates the buffer from the drive signal input.
In an apparatus comprising a second electro-mechanical actuator of the same type as the first actuator, which second actuator carries a second magnetic head, is also mounted on the rotatable body, and is connected to the tracking-signal generator via a second rotary signal coupling means and switching means, the invention may further be characterized in that the bias-voltage input of said second actuator is connected to the bias-voltage input of the first actuator, both bias-voltage inputs have a common connection to the buffer element, and a second voltage isolator is arranged between the drive-voltage input of the second actuator and the bias-voltage input of said second actuator.
With respect to the voltage isolator the invention may further be characterized in that the first or the second voltage isolator comprises a diode which is poled in the forward direction between the relevant drive-voltage input and the relevant signal-voltage input.
A preferred embodiment of the invention may further be characterized in that the two piezoelectric elements arranged on both sides of the common electrode are biased in opposite directions relative to said common electrode, the drive-voltage input is connected to the other electrode of one piezoelectric element and the other electrode of the other piezoelectric element is coupled to earth.
The invention will now be described in more detail, be way of example, with reference to the drawing, in which
FIG. 1 shows an embodiment of the invention,
FIG. 2 shows some signal waveforms to explain the operation of the apparatus in accordance with the invention, and
FIG. 3 shows an alternative to a part of the embodiment shown in FIG. 1.
FIG. 1 shows an embodiment of the invention. On a rotatable body 1, shown schematically, two electro-mechanical actuators 2 and 3 are arranged diame
trally opposite each other, which actuators carry video heads 4 and 5, respectively. Via means, not shown, for example a rotary transformer, these video heads are connected to the non-rotating part of the apparatus. This assembly rotates within a drum around which a magnetic head is wrapped along a helical path over 180° (in said V2000 system). The heads 4 and 5 then alternately follow an inclined track on the magnetic tape. The electro-mechanical actuators 2 and 3 control the heads 4 and 5 in directions indicated by arrows T, i.e. in directions transverse to the direction of the tracks followed by these heads owing to the rotation of the body 1.
The electro-mechanical actuators 2 and 3 each have a common electrode 6, two piezoelectric elements 7 and 8 on both sides of the electrode 6, electrodes 9 and 10 being arranged on both sides of said elements which are remote from the electrode 6, so that the piezoelectric element 7 is arranged between the electrodes 6 and 9 and the piezoelectric element 8 between the electrodes 6 and 10. Both piezoelectric elements are polarized in the direction indicated by P.
In the present example the electrode 10 is connected to earth via the body 1. The common electrode 6 of the actuator 2 or 3 is connected to a drive-signal input, 11 and 12 respectively, which via a slip ring, 13 and 14 respectively, and switching means 15 is connected to a source 18 of tracking signals. Via a capacitor 25 the electrode 9 of the actuator, 2 and 3 respectively, is connected to earth and to a bias-voltage input, 21 and 22 respectively. Via a voltage isolator, in the present example a diode 23 or 24, this bias voltage input, 21 or 22, is connected to the corresponding drive-voltage input 11 or 12. The switching means 15, which may be electr
The operation of the apparatus shown in FIG. 1 will be explained with reference to FIG. 2 which shows the signals S1 and S2 on the slip rings 13 and 14, respectively, as a function of time.
Between the instants t1 and t2 a tracking signal is applied to the slip ring 13. If it is assumed that capacitor 25 carries a higher direct voltage (E), the diode 23 will be cut off. The common electrode 6 of the actuator 2 then receives a signal which appears in parallel across both piezoelements, as indicated by the dashed arrows S, because the electrode 10 is connected directly and the electrode 9 is connected indirectly, via capacitor 25 and via diode 24 and source 20, to earth. In one element the polarity of the signal has the same direction as the polarization (P) and in the other element it is directed oppositely, so that the transducer 2 deflects in conformity with the signal S1. The voltage E across capacitor 25 also appears on the electrode 9. Since the common electrode 6 is connected to the tracking signal source and the electrode 10 is connected to earth, this bias voltage is distributed uniformly as indicated by the arrows V between the two piezoelements in accordance with the polarization P. As a result of this, the neutral level of the actuator (no deflection) is obtained when the voltage on the common electrode 6 is 1/2E (electrode 9 is then at E and electrode 10 at 0 V). The steady-state d.c. level of the tracking signal should then also be 1/2E.
At the same time the direct voltage E from source 20 will appear on slip ring 14 (signal S2). If the charge on capacitor 25 is not sufficient, ca

The same happens between the instants t2 and t3 but now actuators 2 and 3 are interchanged.
It is to be noted that a system is conceivable in which both heads are operative simultaneously, for example in the case of a tape-wrapping angle of 210°, the additional 30° wrap being used for audio recording. Switches 16 and 17 must then be operated so that the voltage E is transferred during a shorter period, for example after the instant t4 as shown in FIG. 2. The switching means 15 must then be modified so that each of the drive inputs 11 and 15 can receive an independent drive signal, at least when both heads are driven simultaneously.
In principle it is also possible to re-charge the capacitor 25 with shorter voltage pulses. The invention may, in principle, also be employed in single-head video recorders.
FIG. 3 shows a possible variant to the device shown in FIG. 1, in which both piezoelectric elements 7 and 8 are polarized in the same direction viewed from the common electrode 6. The drive signal must then be applied to electrodes 9 and 10 in phase opposition in order to obtain a deflection and the bias-voltage input 21 must be connected to the mean voltage across the buffer capacitor 25. Instead of the diode 25 active voltage isolators may then be used.
PHILIPS VR2022S VIDEO2000 Arrangement for the recording and reproduction of wide frequency band video signal:
Method of recording and reproduction of wide frequency band video signals onto or from a magnetizable recording carrier, carried out by the following means: means for separating of the video frequency signals into first and second signals of lower and upper frequency range respectively, for converting said second signal into a third signal the frequency range of which equaling that of said first signal, for frequency modulating a carrier wave frequency by said first and third signals and for recording the frequency modulated signals by means of a twin head, for reproducing the recorded signals by means of a twin head and for amplifying, limiting and demodulating the recorded signals and reconverting the third signal into its original frequency range and combining the so reconverted third signal and said first signal.
1. An apparatus for the recording and reproducing of wide frequency band color video signals onto or from two adjacent tracks of a magnetizable recording carrier, whereat the color video signal to be recorded is separated into a lower and upper frequency range, said lower frequency range frequency modulating a carrier wave, said apparatus further comprising:
a. means for converting said upper frequency range into said lower frequency range;
b. means for frequency modulating said carrier wave by said converted upper frequency range;
c. twin head means for simultaneously recording both said frequency modulated signals; and,
2. The apparatus in accordance with claim 1 wherein the mixing frequency used for the converting and reconverting of the upper frequency range is an integral multiple of the line frequency.
3. The apparatus in accordance with claim 1 wherein the individual recording heads of the twin head have azimuth-angles which are different from zero and are equal in value but oppositely inclined.
In view of the limited band width of the frequency band of simple tape video recording and reproducing apparatuses for home use a color television signal can be recorded only with losses in quality and after a considerable transformation of the original video signals.
For example, in a widely used European system of recording and reproduction, the brightness and chrominance signals are separated from each other. A carrier frequency located at about 4 MHz is frequency-modulated with the brightness signal, which is limited to 2.7 MHz. The chrominance signal is moved out of its original frequency position into a new frequency range, which is located lower than that of the lower side bands of the frequency-modulated brightness signals. Thereafter the frequency-converted color signals are added and recorded.
Japanese systems, which also were developed especially for home use, use essentially the same principle. Both systems suffer from serious disadvantages. The
If guard bands between adjacent tracks are omitted, adjacent tracks are recorded and read at different azimuth angles, and the polarity of the color information is changed from line to line, which requires not only additional electronics but requires a radically different lay-out of the whole electronic circuit, depending upon whether the apparatus is to be used for NTSC, PAL or SECAM.
SUMMARY OF THE INVENTION
It is an object of the present invention to provide a recording and reproducing arrangement for wide frequency band video signals onto or from a magnetizable carrier, which avoids the above described faults and which especially permits the recording of the full video frequency band with small and inexpensive apparatuses and without additional tape consumption at full utilization of the advantages of frequency modulation. The color television system (NTSC, PAL or SECAM) does not influence the recording, so that the same apparatus can be used for all systems, except of course, for different power supply frequencies.
BRIEF DESCRIPTION OF THE DRAWINGS
FIGS. 1 and 2 taken together provide a diagrammatic showing of the subject invention.
DESCRIPTION OF THE PREFERRED EMBODIMENT
An embodiment of the in
vention is shown in the FIGS. in which for example the mean track spacing amounts to 187 μm, the width of a track itself is 130 μm, the frequency modulation deviation ranges from 3.1 MHz to 4.5 MHz, and at this condition video signals up to 2.7 MHz with 10 dB loss can be recorded. If now, according to the invention, the mean track spacing is divided into two tracks each of 93.5 μm track width lying parallel and adjacent to one another without interspace, and if, from the signal which is introduced at connection 1, a lower frequency range extending up to 2.7 MHz is separated by a low-pass filter 2, then this lower frequency range may be frequency modulated in a modulator 3 and after appropriate amplification in an amplifier 4 be recorded by a magnetic transducer head 5, just as well as in the aforementioned original state. Simultaneously, the line synchron im
In the play-back apparatus according to
FIG. 2, the amplifiers 17, the limiters 18 and the demodulators 19, which are following the heads 5 and 15, are once more built wholly alike; the blocks 6, 8, 9, 10 and 11 are the same for recording, according to FIG. 1 and for reproducing, according to FIG. 2. The output voltage of the mixing unit 11 is taken through a band-pass filter 20, which filters out the upper side band of the mixing product, and transfers it to an adder stage 21, which also receives the demodulated signals read by head 5. If necessary, there may be inserted frequency-response corrections at suitable places, deemphasis on offset compensators, and this in both channels.
The synchronization to the line frequency of the mixing frequency of the oscillator 8, which is required for the frequency shift, proves to be especially advantageous, because by this, large time basis deviations are compensated for. The upper cut-off frequency of the demod
As a result, compared with the original shape, the upper useful video frequency can be doubled without loss of playing time or quality, and this, without having to extract the chrominance signal out of the color television signal and without having information carried by the amplitude of the magnetization, which exists at the tape. For this latter reason, the width of the tracks may be further decreased, and in this way, the playing time can be again increased.
Compared with the aforementioned Japanese system, it is true that this system also uses the advantage of abutting tracks. But instead of this
The invention is not limited to the specific oblique track recording, but can also be used at the transverse track, or the longitudinal track methods using rotating magnetic heads. The advantages derived from the invention is independent of the shape (form) of the record carrier and of the track.
PHILIPS VR2022S Method and device for tracking video signals on a magnetic VIDEO2000 SYSTEM tape by detecting phase jumps:
A method and device for maintaining an exact track when playing back video ignals, which are recorded on a magnetic tape in oblique parallel tracks with different azimuth angles.
1. A device for adjusting the exact position of the track when replaying video signals which are recorded in oblique parallel tracks on a magnetic tape, said oblique tracks being alternately recorded and replayed by two rotating heads, the gaps of which have opposite equal azimuth angles causing phase jumps of the line frequency of the scanned video signal during track changes in case of mistracking, said device including means for detecti
2. A device in accordance with claim 1 further comprising means for measuring the phase jumps of the line frequency for changes from an even numbered to an odd numbered track and for changes from an odd numbered to an even numbered track.
3. A device in accordance with claim 2 in which the phase jumps of the line frequency of the video signal with respect to a reference frequency during subsequent track changes are detected by different sample and hold circuits, the outputs of said sample and hold circuits being fed to the input of a differential amplifier to form an error signal, said error signal controlling the tape speed so as to minimize said error signal.
4. A device according to claim 2 further comprising a phase locked loop to produce the reference frequency synchronized to the line frequency of the scanned video signal, said phase locked loop containing a phase comparator, a voltage controlled oscillator and a low pass filter therebetween, said low pass filter causing the control time constant of the voltage controlled oscillator to equal at least the scanning time of one track.
6. A device according to claim 5 in which the error signal of the differential amplifier is added to or subtracted from the rectified voltage of the tacho generator of the tape feed motor and in which by comparing the sum or difference, respectively, with a given reference voltage the rotation of the tape feed motor is controlled so as to minimize the error voltage produced by the differential amplifier.
7. A device according to claim 6 in which a low pass filter is provided at the output of the differential amplifier.
When recording video signals in oblique parallel tracks cross-talking from track to track can be kept to a minimum if the tracks are se
Another possibility for minimizing cross-talk is to record with azimuth angles which differ from track to track. In such a case the guard bands can be eliminated. However, in such a system the requirement for exactly scanning the recorded track is increased.
Methods and devices for an automatical tracking during play-back of video signals in oblique tracks are known, but were never attractive for incorporation into devices for home use. For example it has been suggested to use the time difference which occurs simultaneously with a migration as a measure of the lateral migration of the replay head from the magnetic track. This method can be accomplished by very simple circuitry but poses high demands with respect to the precision and the timely constancy of such circuits, because very small and continuously changing time intervals must be measured.
SUMMARY OF THE INVENTION
The invention is related to video tape recorders where the video signals are recorded in oblique parallel tracks which are alternately recorded and replayed by two rotating video heads with gaps having opposite azimuth angles. The migration of the video heads from the exact track position is determined by the phase jump which occurs during track change.
The invention is based on the realization that the sudden change of a magnitude is easier to measure than a continuous change.
BRIEF DESCRIPTION OF THE FIGURES
FIG. 1 is a diagrammatic representation of two oblique tracks with the tape scanning and tape feeding directions indicated;
FIG. 2 is a schematic diagram utilizing the subject invention; and
FIG. 3 is a schematic diagram illustrating a further embodiment of the invention.
DESCRIPTION OF A PREFERRED EMBODIMENT
FIG. 1 sho
ws two oblique tracks 1 and 2. For track 1 the recording and replay gap of the magnet head is turned from the vertical position counterclockwise through angle α and for track 2 in a clockwise direction through an equal angle α . If during replay the heads are displaced from the nominal position 3, 4 into position 3', 4' by an amount h perpendicular to the track direction, an additional phase change occurs in addition to the reduction of the signal to noise ratio. With the scanning and tape feeding directions and with the azimuth angles of FIG. 1 head 3' scans the video signal by an amount (h) (tan α) earlier and head 4' by an amount (h) (tan α) later than at nominal position. Therefore, during the change from track 1 to track 2 a sudden phase jump takes place corresponding to (2) (h) (tan α) rearwardly and from track 2 to track 1 forwardly. However, if heads 3 and 4 are not migrating upwardly as shown in FIG. 1 but rather downwardly, the sudden phase jump takes place with the magnitude (2) (h) (tan α) forwardly and from track 2 to track 1 rearwardly. Therefore, the magnitude of the phase jump is a measure of the magnitude of migration of the video heads from the track, while the sign of the phase jump determines the direction of migration.
Simultaneously, the scanned line pulses are fed to gate circuits 12 and 13 which open for a short time for about two line durations after each second head change. The necessary opening pulses are fed at 14 and 15 and are derived from the position pulse of the head wheel, so that gate 12 opens when changing from track 1 to track 2, for example, while gate 13 opens when changing from track 2 to the next track.
It is useful to transform the output voltage of oscillator 8 into a trapezoidal wave by pulse former 9 the output of which is fed as a reference to the sample and hold circuits 10 and 16 or 11, 16, respectively. The output signals of 10 and 11 are coupled to the input of differential amplifier 17.
The error signal which is generated at the output of the differential amplifier 17 may be used for making an exact track adjustment for the video heads. For example, the error signal may influence the recovery time of a monostable multivibrator 18 to which the reference pulses for the servo control circuit 20 of the tape transport motor are fed at 19. Another possibility exists in the immediate adjustment of the rotating video heads in axial direction by means of piezoceramic elements which are excited by the error signal of differential amplifier 17.
Since the maintaining of the track and the transport speed for the tape are unmistakeably correlated in accordance with the invention the reference pulses which are fed at 19 may be omitted in accordance with a further embodiment of the invention. In other words, the usual synchronous track is not necessary.
In accordance with FIG. 3, the servo control circuit of band feeding motor 21 includes tacho generator 22 which is coupled with motor 21, and the output voltage of the generator after being rectified at 23 is coupled to the input of a differential amplifier 24. The other input of differential amplifier 24 is coupled to a reference voltage 25. This control loop controls the tape feeding speed approximately to the nominal value, while the output voltage of the differential amplifier 17 which is fed into the summing element 26 provides the exact adjustment of the tape speed with respect to the exact track adjustment.
The additional low pass filter 27, 28 is only necessary for the start of the tape movement and elimates the big alternating phase jumps generated during the acceleration of the magnetic tape.
PHILIPS VR2022S Method for dynamic track adjustment in SYSTEM VIDEO2000 video recorders:.
1. Method for dynamic equidistant track adjustment in magnetic helical-scan video recording with the aid of rotating
1. Verfahren zur dynamischen ·aquidistanten Spureinstellung bei der magnetischen Schr·agspur-Videoaufzeichnung mit Hilfe von rotierenden Video-Magnetk·opfen, die senkrecht zur Bewegungsrichtung durch ein Servosystem verstellbar sind, wobei die Ansteuerung des Servosystems durch ein jeweils am Spuranfang eingetastetes Steuersignal (Burst) bestimmter Freque
2. Verfahren nach Anspruch 1, d a d u r c h g e k e n n z e i c h n e t , dass in jeder zweiten Spur zwischen dem Aufzeichnungs- und Wiedergabebereich des Steuersignals (Burst) eine L·ucke mit der L·ange des doppelten Spurversatzes eingef·ugt ist.
3. Verfahren nach Anspruch 1, d a d u r c h g e k e n n z e i c h n e t , dass in jeder zweiten Spur die Summe der zeitlichen und geometrischen L·ange des Aufzeichnungs- und Wiedergabebereichs f·ur das Steuersignal (Burst) um den doppelten Spurversatz vergr·ossert wird.
Einzelheiten ·uber dieses Verfahren sind beispielsweise aus W Grundig Technische lnforma- tonen", Heft 3/198Q, Seite 111 ff. und "Grundig Technische Infonmationen", Heft 3/1981, Seite 105 ff. zu entnehmen.
Die M·oglichkeit der Steuerung der Magnetk·opfe senkrecht zur Spurrichtung wird ausser zur Spurfindung bei der Wiedergabe aber auch bei der Aufnahme dazu benutzt, um die aufeinanderfolgenden Spuren ·aquidistant zu schreiben.
Hierzu wird ein Schwingungszug, auch Burst genannt, am jeweiligen Spuranfang mit einer weiteren Hilfsfrequenz aufgezeichnet. Unmittelbar nach der Aufzeichnung des Burstsignals, dessen Dauer nach dem Stand der Technik dem von Spur zu Spur entstehenden Spurversatz entspricht, wird der rotierende Magnetkopf auf Wiedergabe umgeschaltet und tastet das Burstsignal der vorhergehenden Spur ab. Die Amplitude des dabei gewonnenen Signals ist ein Mass f·ur den Spurabstand und kann zur Einstellung des rotierenden Magnetkopfes am Spuranfang benutzt werden, derart, dass die Spurabst·ande konstant sind.
F·ur die exakte Spureinstellung darf dabei das Burstsignal nicht zu kurz sein, da mit der nachfolgenden Auswerteschaltung und auch mit der Umschaltung Aufnahme/ Wiedergabe Einschwingvorg·ange mit bestimmter Zeitdauer verbunden sind.
Wird die Aufzeichnung des Burstsignals nach de
m Stand der Technik entsprechend der Dauer des Spurversatzes gew·ahlt, dann liegen die Aufzeichnungsabschnitte in benachbarten Spuren geometrisch treppenf·ormig zueinander wie aus Figur 1 ersichtlich. Der rotierende Magnetkopf kann dann sofort nach der Aufzeichnungsperiode f·ur den Burst auf Wiedergabe umgeschaltet und nach Massgabe des aus der vorhergehenden Spur abgetasteten Burstsignals auf exakten Spurabstand eingestellt werden.
Bei geringer Spurbreite bzw. Bandgeschwindigkeit und entsprechend geringer Spurneigung kann der Spurversatz auf sehr kleine Werte absinken. Entsprechend den oben geschilderten Zusammenh·angen wird dann nach dem Stand der Technik die Dauer des Burstsignals ebenfalls auf einen geringen Wert reduziert. Es besteht dann die Gefahr, dass dieses zeitlich verk·urzte Burstsignal mit R·ucksicht auf die mit der Kopfregelung verbundenen Einschwing- und Urnschaltvorg·ange f·ur eine st·orsichere Regelung nicht mehr ausreicht.
Man k·onnte daran denken, das Burstsignal zeitlich ·uber den Spur versatz hinaus zu verl·angern, um wieder eine sichere Auswertung zu erreichen. Dann aber wandert die geometrische und zeitliche Position des Burstsignals von Spur zu Spur immer weiter auf der Aufzeichnungsspur voran und w·urde schliesslich den Videosignal-Austastbereich verlassen bzw. in den Bildsignalbereich gelangen. Dies ist zur Vermeidung von St·orungen unzul·assig.
Ausserdem l·asst sich bei zunehmender Entfernung der Burstaufzeichnung vom Spuranfang das gew·unschte Ziel der Spureinstellu
Aufgabe der Erfindung ist es, bei der magnetischen Video aufzeichnung in Schr·agspuren auch bei geringem Versatz von Spur zu Spur ein Burstsignal f·ur die Einstellung des Spurabstandes aufzuzeichnen und wiederzugeben, das in seiner zeitlichen Ausdehnung so gew·ahlt werden kann, dass eine sichere Auswertung mit Hilfe der Regeleinrichtung f·ur die Verstellung des Magnetkopfes senkrecht zur Abtastrichtung im Sinne der Erreichung ·aquidistanter Spuren m·oglich ist.
Die erfindungsgem·asse L·osung dieser Aufgabe ist aus Figur 2 ersichtlich. Wird n·amlich die zeitliche Folge der Aufzeichnung und Wiedergabe des Burstsignals von Spur zu Spur alternierend gew·ahlt, dann kann das Burstsignal zeitlich ausgedehnt werden, ohne dass die unerw·unschte Erscheinung der Wanderung innerhalb der Spur in Abtastrichtung auftritt. Im dargestellten Beispiel nach Figur 2 ist in der ersten Spur die geometrische und zeitliche L·ange der Burstaufzeichnung beliebig gew·ahlt. In der folgenden Spur wird nun die Burstaufzeichnung bezogen auf den Spuranfang um die Burstl·ange zuz·uglich des Spurversatzes verschoben und der Lesevorgang vor den Schreibvorgang gelegt. Damit wird der zeitlich verl·angerte Burst vollst·andig ausgewertet und ein neuer Burst mit der gleichen L·ange aufgezeichnet.
In der dritten Spur schliesslich setzt die Burstaufzeichnung bezogen auf den Spuranfang wieder so ein wie in der ersten Spur, w·ahrend der Lesevorgang gegen·uber der Aufzeichnung um die Burstl·ange zuz·uglich des doppelten Spurversatzes verschoben ist. Durch Vertauschung der Reihenfolge von Schreiben und Lesen sowie durch Einf·ugen einer L·ucke zwischen Schreiben und Lesen in jeder zweiten Spur um die Dauer des doppelten Spurversatzes wird also sichergestellt, dass bei verl·angerter Burstdauer das Burstsignal in voller L·ange gelesen werden kann und trotzdem der Schreib- und Lesevorgang am Spuranfang verbleibt, wie es f·ur die wirkungsvolle und st·orsichere Regelung des Spurabstandes n·otig ist.
Ausserdem wird durch
Der zweite Videokopf (geradzahlige Spuren) gibt in festem Abstand oder zeitlicher Dauer vom Spuranfang wieder und zeichnet ohne l·ucke anschliessend auf.
Zum besseren Verst·andnis des Verfahrens sei noch angemerkt, dass die Wiedergabe des Steuersignals (Burst) aus der vorhergehenden Spur trotz Winkelentkopplung auch dann noch m·oglich ist, wenn der Video-Magnetkopf die vorhergehende Spur nicht mehr unmittelbar trifft.
Dies erkl·art sich daraus, dass die Frequenz des Steuersignals bezogen auf das Video signal verh·altnism·assig niedrig gew·ahlt wird, so dass die Winkelentkopplung unwirksam wird und das Streufeld ·uber die Spurbreite hinaus wirkt.
1. Arrangement of rotating toroidal transformers (10, 11) for the inductive transmission of high-frequency oscillations in a video recording and playback machine with at least two signal recording and playback heads (5, 6), which are preferably arranged offset by 180 degrees on a rotating head wheel (2) in a head drum, the transformers each having one rotating (10', 11') toroidal part and one fixed (10", 11") toroidal part, each signal head (5, 6) being assigned the rotating part of a transformer in a certain way, and the transformers (10, 11) being arranged axially one above the other, characterized in that the transformers (10, 11) have different ring sizes such that they do not radially overlap.
1. Anordnung von rotierenden ringf·ormigen Transformatoren zur induktiven ·Ubertragung hochfrequente
r Schwingungen in einem Video-Auf zeichnungs- und -Wiedergabeger·at mit wenigstens zwei Signal-Aufzeichnungs- und Wiedergabek·opfen, die vorzugsweise um 180 versetzt auf einem rotierenden Kopfrad in einer Kopftrommel angeordnet sind, und jedem Signalkopf der rotierende Teil eines Transformators in bestimmter Weise zugeordnet ist, d a d u r c h g e k e n n z e i c h n e t , dass ein Transformator (10) mit rotierendem und feststehendem ringf·ormigem Teil des ersten Signalkopfes (5) gegen·uber dem anderen rotierenden Transformator (11) des zweiten Signalkopf es (6) axial verschoben und durch verschiedene Ringgr·ossen radial und axial nicht ·uber schneidend in der Kopftrommel (1) angeordnet ist.
2. Anordnung nach Anspruch 1, d a d u r c h g e k e n n z e i c h n e t , dass das Kopfrad (2) einen hochgezogenen Flansch (13) aufweist, auf den ein rotierender Trafoteil (11) aufgesetzt ist, w·ahrend der andere rotierende Trafoteil mit der geringeren Ringgr·osse (10') auf der inneren Planseite des Kopfrades (14) angeordnet ist, und die H·ohe des Flansches wenigstens der gesamten Querschnittsh·ohe eines Transformators entspricht.
3. Anordnung nach Anspruch 2, d a d u r c g e k e n n z e i c h n e t , dass die H·ohe des Flansches des Kopfrades der halben Querschnittsh·ohe des kompletten Transformators entspricht.
Bei den meisten bekannten magnetischen Bild-Aufzeichnungs- und Wiedergabeger·aten mit bandf·ormigem Aufzeichnungsmedium erfolgt die Aufzeichnung und Wiedergabe der Video signale auf das Magnetband mittels sogenannter Schr·agspuraufzeichnung bzw. Abtastung ·uber auf einem rotierenden Kopfrad angeordnete Videok·opfe.
Es ist bekannt, dass hierbei die hochfrequenten Schwingungen mit Hilfe eines rotierenden Transformators induktiv ·ubertragen werden. Da vorzugsweise mit zwei um 1800 auf dem Kopfrad versetzt angeordneten Videok·opfen gearbeitet wird, sind auch hierzu zwei getrennte rotierende Transformatoren erforderlich. Das Kopfrad mit den beiden Videok·opfen ist mit den rotierenden Transformatoren in einer vom Magnetband teilweise umschlungenen zweigeteilten Kopftrommel integriert, wobei wenigstens ein Teil der Kopftrommel feststeht. Die Unterbringung der beiden rotierenden Transformatoren erfolgt in bekannter Weise in der Kopftrommel derart, dass diese entweder axial ·ubereinander angeordnet sind, oder sich mit verschiedenen Radien der einzelnen ·Ubertragerringe in einer Ebene befinden.
Ein wesentlicher Unterschied dieser verschiedenen Anordnungen ergibt sich in der Bewertung der Ubersprechd·ampfung von einem zum anderen rotierenden Transformator. Eine messwertm·assig grosse Obersprechd·ampfung ist bei Ger·aten der geschilderten Art in zunehmender Weise w·unschenswert, da inzwischen auch das Stereo-Tonsignal im Schr·agspurverfahren aufgezeichnet bzw. abgetastet wird.
Es kann somit in Videoaufzeichnungsger·aten ein PCM Tonsignal in einer Zusatzumschlingung vor oder nach der Video spur aufgezeichnet werden. Besonders hohe Anforderungen an die ·Ubersprechd·ampfung zwischen den beiden rotierenden Signal·ubertragern (Transformatoren) werden dann noch gestellt, wenn bei dieser genannten Tec
Aufgabe der Erfindung ist es daher, eine Anordnung und Ausf·uhrung von wenigstens zwei rotierenden Transformatoren in Videoaufzeichnungsger·aten zu schaffen, die einerseits ein gutes ·Ubersprechverhalten sicherstellt und andererseits einen einfachen konstruktiven Einbau der rotierenden Transformatoren in die Kopftrommel des Ger·ates gew·ahrleistet.
Diese Aufgabe wird erfindungsgem·ass durch die im kennzeichnenden Teil des Anspruchs 1 angegebenen Merkmale gel·ost.
Vorteilhafte Ausgestaltungen des erfindungsgem·assen Aufbaus eines rotierenden ringf·ormigen Transformators in einer Kopftrommel f·ur Videoaufzeichnungsger·ate ergeben sich aus den Unteranspr·uchen.
Ein Ausf·uhrungsbeispiel wird nachfolgend anhand einer schematischen Zeichnung n·aher erl·autert.
Die Anschl·usse der Signalk·opfe werden jeweils ·uber eine Kontaktplatte 12, die sich im oberen Teil der Kopftrommel befindet, zu den Transformatoren 10 und 11 gef·uhrt. Die rotierenden Transformatoren bestehen, wie bekannt, aus zwei Ringkernh·alften mit eingelegten Wicklungen, wobei der jeweils rotierende Teil 10' und 11' an dem Kopfrad und der feststehende Teil 10'' und 11'' am unteren Teil der Kopftrommel befestigt ist. Die beiden Ringteile sind durch einen sehr kleinen Luftspalt getrennt. Die Anschl·usse der feststehenden Trafo-Ringteile werden in einfachster Weise ·uber Bohrungen, die sich im unteren Teil der Kopftrommel befinden, an eine nicht n·aher dargestellte Schaltungsplatte gef·uhrt.
Nach der Zeichnung ist der Transformator 10, der dem ersten Signalkopf 5 zugeordnet ist, gegen·uber dem anderen Transformator 11, der dem zweiten Signalkopf 6 zugeordnet ist, axial verschoben und durch verschiedene Ringgr·osse radial und axial nicht ·uberschneidend in der Kopftrommel angeordnet. Um diese Anordnung zu erreichen, weist das Kopfrad 2 einen ·ausseren hochgezogenen Flansch 13 auf, an dem der rotierende Trafoteil 11' des Trafos 11 (mit grossem Ringdurchmesser) befestigt ist. Der rotierende Trafoteil 1

Eine andere nicht dargestellte Anordnung sieht eine Flanschh·ohe vor, die etwa nur der halben Querschnittsh·ohe des Transformators entspricht.
PHILIPS VR2022S System for extending the playing time of video cassettes in VIDEO2000 SYSTEM.
A system is provided for extending the playing time of standardized video cassettes. The system utilizes a rotating head drum having mounted thereon a first set of video heads displaced 180° with respect to each other, a second set of video heads displaced by a certain amount from 180° with respect to each other, a rotating winding of a transformer, and relays to interconnect the heads of either the first or second set of heads with the rotating winding as the head drum rotates. The relays are controlled by stationary coils and logic to respond to the setting of switches to enable the system to operate at normal tape speed via the first set of heads or reduced tape speed via the second set of heads without requiring any change in the speed of rotation of the head drum.
1. In a video tape record/playback machine of the type including a tape transport, a tape transport drive, a rotating head drum, means for rotating said head drum, a first pair of video heads mounted on said head drum and displaced from each other by 180°, and a transformer having a rotating winding mounted to said head drum and a stationary winding; the improvement comprising: a second pair of video heads mounted to said head drum and displaced from each other by an angle slightly different from 180° and control means to interconnect said first pair of video heads and said rotating winding when said tape transport drive is operated at a normal speed and to interconnect at least one of the video heads of said second pair and said rotating winding when said tape transport drive is operated at a lower, extended play speed.
2. The machine in accordance with claim 1 wherein said control means comprises: a first polarized relay affixed to said head drum for rotation therewith, said first relay having a first positi
first and second stationary exciter coils in controlling relationship with said first relay to drive said first relay to said first or second position;
switch means having a "normal" position and a "long play" position; and
logic circuit means responsive to the "normal" or "long play" position of said switch means to activate said exciter coils to drive said first relay to said first or second position respectively.
3. The machine in accordance with claim 2 wherein said second pair of video heads comprises a record/playback head and a playback only head; said switch means further has a "record" position and a "playback" position and further comprising
a second polarized relay affixed to said head drum for rotation therewith and having a "playback" position interconnecting both heads of said second pair of video heads with said rotating winding and a "record" position interconnecting only said record/playback head with said rotating winding;
said first and second stationary exciter coils are in controlling relationship with said second relay to drive said second relay to said "record" or "playback" position; and
4. The machine in accordance with claim 3 wherein said switch means further includes a "start" position indicating that said tape transport drive has been activated and said logic circuit means is responsive to said "start" position of said switch to activate said exciter coils to drive said first relay to said first position regardless of whether said switch is in said "normal" or "long play" position.
5. The machine in accordance with claim 1 further comprising a servo control connected to said tape transport drive, a tachometer generator secured to said tape transport drive adapted to generate pulses responsive to the rotational speed of said drive; a tape transported past said head drum by said tape transport, said tape having thereon first and second slant tracks, and the nominal output of said tachometer generator at said normal and lower speeds are integral multiples of the frame frequency of said slant tracks.
6. The machine in accordance with claim 5 further comprising: a divider connected to the output of said tachometer generator, said divider having a first state to divide the output of said tachometer generator by a first fixed integer to reduce it to the frame frequency when said tape transport operates at normal speed and a second state to divide the output of said tachometer generator by a second fixed integer to reduce it to the frame frequency when said tape transport operates at a lower speed;
a comparator having a first input from said divider, a second input from a reference pulse source, and an output in controlling relationship with said servo control;
a reference pulse source; and
means for switching said reference pulse source between a first state to generate reference pulses corresponding to said normal speed and a second state to generate reference pulses corresponding to said lower speed.
7. Video tape cassette recorder provided for the use of standardized video cassettes and for extending the playing time of said video cassettes, said recorder including a tape transport mechanism capable of driving the tape at a normal standardized speed and at essentially half the standardized speed, a rotating head drum with a first pair of video heads displaced from each other by 180° and with a second pair of video heads displayed from each other by an angle slightly different from 180° and displaced from said first pair by a suitable angle; a transformer with one stationary winding and one rotating winding mounted to said head drum, said head drum being equipped with a first polarized relay to connect said first or said second pair of video heads to said rotating transformer windin
8. A video tape cassette recorder in accordance with claim 7 wherein said operative switches include a special switch for the start and the stop of the tape transport drive; said special switch being interconnected with said logic circuits so as to connect in the stop position of said special switch said first pair of video heads to said rotating transformer winding regardless of whether said respective operative switch is in the normal or in the long play mode position.
9. A video tape cassette recorder in accordance with claim 7 further comprising a tachometer generator and a frequency divider for the output pulses of said tachometer generator; said tachometer generator being secured to and producing a plurality of pulses per revolution of said tape transport drive; the frequency of said tachometer generator output pulses being an integral multiple of the frame frequency of the video signal at both the rated normal and the rated low speed of said tape transport drive; and said frequency divider being switchable between two division factors so as to divide to frame frequency the frequency of said tachometer generator output pulses at both, the rated normal and the rated low speed of said tape transport drive.
The present invention relates to video tape recording and more particularly to a system for extending the playing time of standardized video cassettes in which each of two rotating video heads, displaced relative to each other by 180°, records or scans one slant track per television field.
As a result of the above established standards, the maximum playing time of a cassette is limited to about an hour utilizing the thinnest tapes available. This playing time is not sufficient for certain forms of desired programs (e.g., such as full-length motion pictures). Thus, a considerable need exists for a system to extend the playing time of a standard cassette while maintaining provision for normal recording and playback capabilities.
It has heretofore been proposed (in German Pat. No. 1,437,141 for example) that the playing time of a given length of tape could be extended through the slant track method by recording only the even or odd television fields but scanning them twice during playback with the tape transport moving at roughly half the normal speed. In practice, a head drum which rotates at 1500 RPM and carries two video heads is utilized. The magnetic tape is looped 180° over the head drum. For recording, only one of the heads operates while for playing back both heads scan the same track. It is also known that in this case the two heads must no longer be precisely 180° apart from each other but the additional head position must be displaced by a slight amount from 180°. In practice this displacement distance is on the order of a millimeter and thus, it would not be practical to mount an additional head displaced by this slight amount.
The principal object of the present invention is to provide an improved video cassette machine capable of functioning in both a standard normal mode and an extended play mode.
A further object is to provide such a machine which can be readily switched from one mode to the other without requiring any intervention with the drive mechanism of the head drum.
SUMMARY OF THE INVENTION
The above an
BRIEF DESCRIPTION OF THE DRAWINGS
In the accompanying drawings:
FIG. 1 is a schematic of the head drum and its control logic;
FIG. 2 is a circuit diagram of the switching arrangement between the normal and long playing heads; and
FIG. 3 is a schematic of the tape speed switching arrangement.
DETAILED DESCRIPTION OF THE PREPARED EMBODIMENT
Reference is now made to the drawings wherein similar components bear the same reference numeral throughout the several views.
In FIG. 1, a rotating drum head 1 is shown carrying a first set of heads N1 and N2 displaced 180° apart from each other f1 could theoretically be used with another head displaced slightly apart from N2 by a distance on the order of 1 millimeter. Since this is not practical to effect, a second set of heads L1 and L2 is mounted to the head drum with the displacement between heads L1 and L2 being off slightly from 180° as shown. The arrows adjacent to the heads N1, N2, L1 and L2 depict their operability. Accordingly, heads N1, N2 and L1 are designed for record and playback operation while head L2 is designed for playback operation only.
or normal (N mode) operation. For long playing (L mode) operation head N
Referring briefly to FIG. 2, it can be seen that a rotating transformer 2 is provided with one rotating winding and one stationary winding. Since rotating multiple transformers are expensive, only a simple transformer 2 is provided. As shown in FIG. 1, a small polarized relay 3 rotates with the head drum and serves to connect the rotating winding of the transformer with heads N1 -N2 or L1 -L2 as required. To this end, the relay 3 is switched by stationary exciter coils 4 and 5 as the head drum rotates. A second polarized relay 6 is also provided to connect both heads L1 and L2 to the transformer winding during L mode-playback but only head L1 to the transformer winding during L mode-record. The electrical contacts of the polarized relays 3 and 6 are shown in FIG. 2.
The logic and switches for the control of the polarized relays 3 and 6 is depicted in FIG. 1. Thus, as shown, coil 4 is energized by the output of AND gates 7 or 8. Coil 5 is energized by the output of AND gates 9 or 10. In turn, each of the AND gates 7, 8, 9 and 10 has an input from the function switches 11 used to determine (a) L or N mode; (b) record or playback; and (c) whether the tape transport is operative or not.
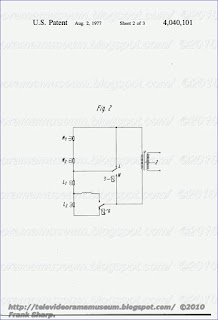
The output of pickup 13 is also delayed 20 ms through delay means 12 and then applied to gates 8 and 10. 20 ms corresponds to the time it takes for the drum head 1, rotating at 1500 RPM, to rotate through 180°. Thus, 20 ms or half a head drum rotation after relay 3 is excited by coils 4 or 5, relay 6 is excited by coils 4 or 5.
In N mode (i.e., switch 11 at N position) the electrical contacts of relay 3 are switched to N thereby connecting the heads N1 and N2 in series with the rotating transformer. The position of the contacts of relay 6 is immaterial since in N position relay 3 shunts past heads L1 and L2. The operation of the cassette system then proceeds in a conventional manner.
In L mode -- record, (switch 11 at L and "record") the electrical contacts of relay 3 are switched to the L position via the AND gate 15, the OR gate 16 and AND gate 9. After 20 ms, relay 6 is energized via gates 15 and 8 and the head L1 is thereby connected to rotating transformer 2.
In L mode -- playback (switch 11 at L and "playback") one must differentiate between the tape in the running or stopped condition. The latter would occur, for example, for the reproduction of still pictures. It has been found that with the magnetic tape stopped, even when in the "L" mode, the N heads must be utilized since the L heads will incorrectly scan the tracks resu
When the tape drive is started (and switch 11 is thus in the L mode -- playback, tape start position) the relay 3 is switched to the L position via AND gate 19, OR gate 16 and AND gate 9. In addition 20 ms later relay 6 is energized to the playback position via AND gate 10 so that the two heads L1 and L2 are connected in series with the transformer coil 2.
In both the N and L modes of operation the start of each slant track has to coincide with the start of a field and hence phase control of the head drum 2 is required. This is accomplished by means of a phase comparator 20 which compares pulses from the pickup 13 with reference pulses from an outside reference source 21. The reference pulses could, for example, comprise the vertical synchronous pulses separated from the video signal. The output of the comparator 21 is fed to an amplifier 22 which feeds the drive motor 23 of the head drum 1.
A phase shifter 24 is provided between the comparator 20 and pickup 13 to compensate for tolerances of the apparatus. The phase difference corresponding to the angle α in FIG. 1 which occurs in the transition from N to L operation is compensated for via switch 25.
In the present case with a track spacing in N-operation corresponding to 11 half-lines, a track spacing corresponding to five whole lines must therefore be chosen in L-operation, i.e., the speed of rotation of the transport shaft must be reduced in the ratio of 5:11. The frequency of the pulses delivered by the tachometer generator is thereby also decreased in the ratio of 5:11.
In order to carry out the switching of the speed between N- and L- operation as simply as possible and, also, by purely electrical means, the number of tachometer pulses per revolution of the transport shaft is chosen so that the tachometer pulse frequencies which occur at the desired speed of the magnetic tape in N- and L- operation are integral multiples of the frame frequency. If, therefore, Z is the number of tachometer pulses per revolution of the transport shaft, and if nN and nL are its speed of rotation in N- and L-operation, the following is to apply: Z . nN = p . 25 and Z . nL = q . 25,
where p and q are integral numbers and 25 Hz is the frame frequency. Since the ratio of the speeds of rotation is the same as that of the line numbers corresponding to the track spacings, therefore, in the example above nN /nL = 11/5 and p/q = 11/5.
FIG. 3 shows the circuit diagram of the transport shaft control and of the transport speed switching arrangement. For simplicity, only the recording operation is shown. Motor 26 drives the magnetic tape in the direction of the arrow via the transport shaft 27 and a rubber pressure roller (not shown). A tachometer generator is coupled to the transport shaft. This may consist of a ferromagnetic gear 29 and a pickup 30 which generates pulses in response to rotation of the gear. The tachometer pulses are fed via an amplifier 31 to a frequency comparator 32 and a switchable frequency divider 33. The time constant of an R-C circuit or the charging time of a capacitor can serve as the reference for comparator 32. Both of these can be adjusted by simple means via the double-throw switch 34 to the pulse frequencies coming from pickup 30 in N- or L-operation. A divider 33 divides the tachometer pulse frequency down to the frame frequency, where the division ratio can be changed by means of switch 35 from p:1 in N-operation to q:1 in L-operation. The actual frame frequency appearing at the output of divider 33 is phase-compared in comparator 36 with the reference frame frequency and the error signal so produced also serves as an input to control the frequency comparator 32.
The reference frame frequency is obtained in the frequency divider 37 by halving the vertical blanking frequency, which is separated from the video signal to be recorded and is fed to the terminal 38. This frame frequency is recorded at the same time on the tape 28 as the sychronization track 40 via the stationary magnetic head 39. The resulting error signal produced in 32 controls the motor 26 via the control amplifier 41.
With the numbers given above, the number of teeth of the ferromagnetic gear tachometer 29 can, for example, be chosen as 110. If the desired speed of rotation of the motor 26 is 750 RPM in N-operation, p = 55 and q = 25 for the divider 33.
The switches 34 and 35 shown in FIG. 3 can be ganged to operate together with the N/L switch 11. To prevent operating errors, it is advisable, however, to operate the switch 25 via the control logic rather than manually.
Thus in accordance with the above, the aforementioned objectives are effectively attained.
PHILIPS VR2022S Device for the track following of rotating magnetic heads SYSTEM VIDEO2000.(DYNAMIC TRACK FOLLOWING)
1. Einrichtung f·ur die Spurnachf·uhrung von rotierenden Magnetk·opfen in Magnetbandger·aten, bei der als Tr·ager der Magnetk·opfe Piezoelemente verwendet sind, die an einem Ende fest in einer rotierenden Halterung eingespannt und an ihrem auslenkbaren Ende mit dem Magnetkopf verbunden sind, d a d u r c h g e k e n n z e i c h n e t , dass zur Erh·ohung der Auslenkung die freie L·ange (b) der Piezoelemente (4, 5) schr·ag zur Verbindungslinie (6, 7) zwischen zugeordnetem Magnetkopf (2, 3) und Drehpunkt (8) der rotierenden Halterung (1) bis etwa in der H·ohe dieses Drehpunktes verl·auft, und dass zur Kompensation von Azimutfehlern die Piezoelemente schr·ag (a1, a2) in die rotierende Halterung eingespannt sind.
2. Einrichtung nach Anspruch 1, d a d u r c h g e k e n n z e i c h n e t , dass die rotierende Halterung der Piezoelemente fest mit einem rotierenden Kopfrad (1) verbunden ist.
indung betrifft eine Einrichtung f·ur die Spurnachf·uhrung von rotierenden Magnetk·opfen in Magnetbandger·aten, bei der als Tr·ager der Magnetk·opfe Piezoelemente verwendet sind, die an einem Ende fest in einer rotierenden Halterung eingespannt und an ihrem auslenkbaren Ende mit dem Magnetkopf verbunden sind.
Seit einiger Zeit werden beispielsweise in Videorecordern zur Spurnachf·uhrung Piezoelemente (in diesem Zusammenhang auch "Aktuatoren" oder Bimorphe" genannt) verwendet, an deren freischwingenden Enden die Magnetk·opfe befestigt sind. Die Piezoelemente weisen die Eigenschaft auf, dass sie beim Anlegen einer Spannung je nach Polarit·at in die eine oder andere Richtung ausgelenkt werden, so dass die Magnet k·opfe senkrecht zur Abtastrichtung bewegt werden k·onnen. Steuert man die Piezoelemente mit einer Regelspannung entsprechend dem Spurfehler an, so folgen die Videok·opfe genau den vorgesehenen Spuren.
An ihren anderen Enden sind die Piezoelemente fest in einen Piezoeiementhalter eingespannt, der entweder selbst rotiert oder starr mit dem rotierenden Kopfrad des Videorecorders verbunden ist. Die freischwingende L·ange des Piezoelementes ist ein Mass f·ur die erreichbare Kopfauslenkung.
Die Figuren 1 und 2 zeigen bekannte Anordnungen zur Spurnachf·uhrung in Videorecordern. Die Magnetk·opfe 2 und 3 sind an den freischwingenden Enden der Piezoelemente 4 und 5 befestigt (z. B. aufgeklebt). Die freischwingenden L·angen der Piezoelemente sind mit b bezeichnet. An ihren anderen Enden sind die Piezoelemente in einen Piezoelementhalter 1 eingespannt, der entweder selbst als rotierendes Teil ausgebildet oder mit dem rotierenden Kopfrad des Videorecorders starr verbunden ist. Die Einspannl·ange der Piezoelemente in die Piezoelementhalter ist mit a bezeichnet.
Neuere Trends in der Video technik f·uhren zu immer klein
Der vorliegenden Erfindung liegt deshalb die Aufgabe zugrunde, eine Einrichtung zur Erh·ohung der Piezoelementauslenkung zu schaffen, die sich insbesondere f·ur kleine Magnetbandger·ate eignet, billig ist und eine praktisch azimutfehlerfreie Wiedergabe der magnetisch aufgezeichneten Signale erm·oglicht.
Diese Aufgabe wird nach der vorliegenden Erfindung dadurch gel·ost, dass die Piezoelemente schr·ag zur Verbindungslinie zwischen zugeordnetem Magnetkopf und Drehpunkt der rotierenden Halterung bis etwa in die H·ohe dieses Drehpunktes verlaufen und dass die Piezoelemente zur Vermeidung von Azimutfehlern schr·ag in die rotierende Halterung eingespannt sind.
Die Vorteile der Erfindung liegen darin, dass insbesondere bei Magnetbandger·aten mit kleinen Kopfr·adern die freischwingenden L·angen der Piezoelemente und damit die erreichbare Auslenkung vergr·ossert wird.
Im folgenden wird ein Ausf·uhrungsbeispiel f·ur die vorliegende Erfindung mit Hilfe der Figur 3 n·aher erl·autert. Die Magnetk·opfe 2 und 3 sind an den freischwingenden Enden der Piezoelemente 4 und 5 befestigt. Die freischwingenden L·angen'der Piezoelemente sind mit b bezeichnet.
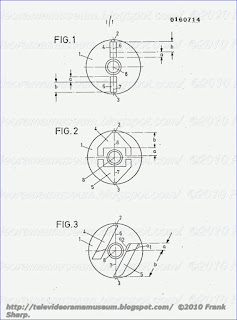
Diese Einspannung erfolgt im Gegensatz zum Stand der Technik schr·ag, um die sonst bei der Auslenkung der Piezoelemente zu erwartenden Azimutfehler der Magnetk·opfe zu kompensieren. Damit wird eine praktisch azimutfehlerfreie Wiedergabe der magnetisch aufgezeichneten Signale erm·oglicht. Die Einspannl·ange, unter der hier der Mittelwert der Strecken al und a2 verstanden wird, ist mit a bezeichnet.
Mit einer Anordnung nach der vorliegenden Erfindung wird erreicht, dass im Vergleich zum Stand der Technik bei sonst gleichen Bedingungen (insbesondere bei gleicher Regelspannung)die erreichbare Auslenkung der Piezoelemente vergr·ossert wird.
Die Erfindung ist nicht auf das vorliegende Ausf·uhrungsbeispiel beschr·ankt. Beispielsweise spielt es keine Rolle, welcher Art die Verbindungen zwischen Magnetkopf und Piezoelement sowie Piezoelement und Piezoelementhalter sind.
recordern mit einem rotierenden Kopfrad, wobei die Magnetk·opfe an Piezoelementen befestigt sind und jeder Kopf w·ahrend einer Vollumdrehung des Kopfrades eine Bandeingriffphase und eine Nichteingriffphase hat, und wobei an das Piezoelement eines Kopfes, der gerade imBandeingriff steht, eine Spannung angelegt wird, die den Kopf auf der vorgesehenen Spur h·alt, und wobei an das Piezoelement eines Kopfes, der gerade nicht im Bandeingriff steht, eine abklingende Wechselspannung zur Beseitigung des Hystereseeffektes des Piezoelementes angelegt wird.
Seit einiger Zeit werden in Videorecordern zur exakten Spurhaltung Piezoelemente (in diesem Zusammenhang auch "Aktuatoren" oder Eimorphe" genannt) verwendet, auf denen die Ma
Aus der europ·aischen Offenlegungsschrift mit der Publikationsnummer 0091 750 ist eine Anordnung zur Spursteuerung bekannt, bei der ein auf einem Piezoelement befestigter Magnetkopf w·ahrend der Bandeingriffsphase durch das Anlegen einer positiven oder negativen Gleichspannung an eine vorgegebene Stelle gebracht wird. Nach dem Abschalten dieser Gleichspannung am Beginn der Nichteingriffsphase kehrt die Kopf-Piezoelement-Einheit nicht wieder exakt in ihre Ausgangsposition zur·uck, da aufgrund des Hystereseeffektes im Piezoelement eine Restauslenkung verbleibt, die die Nullpunktlage der Kopf-Piezoelement-Einheit ver·andert. Demzufolge werden bei der n·achsten Bandeingriffsphase dieses Kopfes Spurfehler auftreten.
Um diese m·oglichst schnell auszuregeln, ·uberlagert man der an das Piezoelement angelegten Gleichspannung w·ahrend der Nichteingriffsphase eine abklingende sinusf·ormige Wechselspannung. Nach dem Abklingen dieser sinusf·ormigen Wechselspannung liegt am Piezoelement die Spannung an, die die jeweils geforderte Ablenkun
Des weiteren ist aus der europ·aischen Offenlegungsschrift mit der Publikationsnummer 0091 764 eine Vorrichtung bekannt, die ebenso wie der Erfindungsgegenstand zur Spurregelung den Piezoeffekt ausnutzt.
Bei der bekannten Vorrichtung sind zwei um 180 Grad versetzte Magnetk·opfe an Piezoelementen befestigt, die ihrerseits fest mit dem Kopfrad verbunden sind.
Zur Vermeidung eines Spurfehlers bei im Vergleich zur Aufzeichnung unterschiedlicher Wiedergabegeschwin digkeit wird an die beiden Piezoelemente w·ahrend des jeweilyFn Bandeingriffs ein dreieckf·ormiges Spurkorrektursignal angelegt. W·ahrend des Nicht eingriffs beh·alt das Piezoelement und damit auch der daran befestigte Magnetkopf eine Restauslenkung, so dass auch bei dieser Anordnung die Nullpunktlage der Kopf Piezoelement-Einheit ver·andert wird, was am Beginn der n·achsten Bandeingriffsphase des Magnetkopfes zu einem Spurfehler f·uhrt.
die Wiedergabegeschwindigkeit kleiner oder gr·osser als die Aufzeichnungsgeschwindigkeit war, dem Piezoelement eine geeignet gepolte Spannung zur Beseitigung von Hystereseefekten zuf·uhrt. Es zeigt sich also, dass der Versuch, die Hystereseefekte ohne Verwendung, einer Umpolvorrichtung f·ur die abkleme Weckselspannung zu beseitigen, noch keine zufried stellenden Ergebnisse bringt.
Ausgehend von diesem Stand der Technik liegt der vorliegenden Erfindung die Aufgabe zugrunde, eine verbesserte Anordnung zur Beseitigung von Hysterese- effekten einer Kopf-Piezoelement-Einheit zu schaffen, mit der auch ohne Verwendung einer Umpolvorrichtung die Hystereseefekte der Kopf-Piezoelement- Einheit vollst·andig beseitigt werden.
Die L·osung dieser Aufgabe erfolgt durch die kennzeichneneden Merkmale des Patentanspruchs.
Die Vorteile der Erfindung liegen nicht nur darin, dass die Videnkopfe am beginn ihrer n·achsten Bandeingriffsphase an ihrer Sollposition stehen, sondern in der mehrere auch darin dass eine Desensibilizierung der Piezoelment verwenden wird, also keine Verringerung der Empfindlichkeit gegen·uber der angeleg ten Spannung auftritt, was bei einem l·angeren Anlie gen einer Spannung (insbesondere einer hohen Gleich spannung) an einem Piezoelement der Fall sein k·onnte.
im folgenden wird die Erfindung an einem Ausf·uhrungs beispiel n·aher erl·autert. Dabei zeigen: Fig. 1 ein Blockschaltbild mit allen f·ur die Erfindung wesentlichen Bauteilen und Fig. 2 ein Diagramm, das die Verl·aufe der an die Piezoelemente angelegten Spannun gen als Funktion der Zeit zeigt.
Im Ausf·uhrungsbeispiel von Figur 1 wird dem Eingang A eines Microcomputers 1 eine auf bekannte Art und Weise erzeugte digitale, impulsbreitenvariable Regelspan nung zugef·uhrt, die eine genaue Auskunft ·uber die Ab weichung des jeweiligen Magnetkopfes von der Soll spurlage gibt. Eine detaillierte Beschreibung der Er zeugung einer derartigen Regelspannung kann beispielsweise der Zeit schrift "Grundig Technische Informationen" 3/81, S. 110 - 116, entnommen werden.
Der Microcomputer 1 erzeugt an seinem Ausgang B vom jeweiligen Betriebszustand (Aufzeichnung, Wiedergabe, Zeitlupe, Zeitraffer) abh·angige digitale Regelsignale f·ur die ?iezemente. Die
Der Schalter 5 befindet sich w·ahrend dieser Zeitspanne in der Stellung b, so dass die am Ausgang des D/A-Wandlers 2 anliegende Regelspannung ·uber die Schalter 3 und 5 an das Piezoelement 1 weitergegeben wird und der am Piezoelement 1 befestigte Magnetkopf der durch die Regelspannung vorgegebenen Spur folgt.
Ist die Kopf-Piezoelement-Einheit 1 im Bandeingriff, dann befindet sich die Kopf-Piezoelement-Einheit 2 in ihrer Nichteingriffsphase. Diese Zeitspanne wird ausgenutzt, um dem Pie
Damit wird eine eventuelle Restauslenkung des zugeharigen Magnetkopf es, die ihre Ursache in der Hysterese im Piezoelement 2 hat, vollst·andig beseitigt. Besonders wirkungsvoll ist gem·ass einem Merkmal der Erfindung die Beseitigung der Hystereseeffekte des Piezoelementes dann, wenn die Frequenz der angelegten Rechteckspannung knapp unterhalb der mechanischen Resonanzfrequenz (ungef·ahr 1 kHz) des Piezoelementes liegt, also beispielsweise in der Gr·ossenordnung von 700 Hz.
Hat der Magnetkopf 1 die Spur zuende gelesen bzw.
Der Schalter 3 ist in dieser Phase ge·offnet. Gleichzeitig dazu wird dem Piezoelement 1 ·uber den Schalter 5, der sich in dieser Phase in der Stellung a befindet, eine abklingende Rechteckspannung von einem vom Microcomputer 1 gesteuerten Generator 8 zur vollst·andigen Beseitigung des Hystereseeffektes des Piezoelementes 1 zugef·uhrt, die eine eventuelle Restauslenkung der Kopf-Piezoelement-Einheit 1 beseitigt, so dass der Magnetkopf 1 am Beginn seines n·achsten Bandeingriffes an der richtigen Stelle steht.
Figur 2 gibt einen ·Uberblick ·uber
die an die Piezoelemente 1 und 2 angelegten Spannungen. Dabei entsprechen die Zeitintervalle [ t1, t2 ] , [ t3 > t4 ] > [ t5, t6 ] , den Bandeingriffsphasen der Kopf-Piezoelement-Einheit 1 und den Nichteingriffsphasen der Kopf-Piezoelement Einheit 2 und die Zeitintervalle [ t2, t3 ] [ t4, t5 [ t6, t7 ] , den Bandeingriffsphasen der Kopf-Piezoelement-Einheit 2 und den Nichteingriffsphasen der Kopf-Piezoelement-Einheit 1.
Die obengenannten Zeitintervalle, die f·ur die Beseitigung der Hystereseeffekte der Piezoelemente 1 bzw.
2 zur Verf·ugung stehen, liegen bei Verwendung von zwei um 180 Grad versetzten Magnetk·opfen im Normalbetrieb bei 20 msec. Es hat sich ·uberraschenderweise gezeigt, dass eine Beseitigung der Hystereseeffekte der Piezoelemente besonders wirkungsvoll ist, wenn die-Frequenz der Spannung zur Beseitigung der Hystereseeffekte knapp unterhalb der mechanischen Resonanzfrequenz der Piezoelemente gew·ahlt wird, die in der Gr·ossenordnung von 900 - 1200 Hz liegt, und eine abklingende Rechteckspannung verwendet wird. Bei der Wahl der Frequenz muss lediglich darauf geachtet werden, dass keine st·orenden Resonanzerscheinungen auftreten, d. h. dass die Frequenz nicht zu nahe bei der mechanischen Resonanzfrequenz der Piezoelemente liegt.
W·ahlt man beispielswelse 700 Hz, dann betr·agt die Dauer einer S
Der exakte Verlauf des Abklingvorganges (Verlauf der Einh·ullenden der abklingenden Rechteckspannung) richtet sich nach den physikalischen Eigenschaften des jeweils verwendeten Aktuatormaterials. Es ist in jedem Fall darauf zu achten, dass die Amplitude der letzten Rechteckschwingung hinreichend klein gew·ahlt wird.
Dies kann eine Desensibilisierung der Piezoelemente gegen·uber der angelegten Spannung zur Folge haben, d. h. die Piezoelemente k·onnen dann, wenn ·uber einen l·angeren Zeitraum eine hohe Gleichspannung--an ihnen anliegt-, gegen·ubn der angelegten Spannung unempfindlich werden, so dass Spurfehler entstehen. Auch dieser Nachteil wird durch eine Beseitigung der Hystereseeffekte nach der vorliegenden Erfindung in vorteilhafter Weise vermieden.
The present invention relates to video recording and in particular to reproducing still pictures recorded along slant tracks on magnetic video tape.
When reproducing still pictures recorded on slant tracks on magnetic tape it is common practice to repeatedly scan the same slant track with the rotating head or heads. This is particularly true for the widely used devices wherein a field is recorded per slant track with two 180° offset video heads. The two video heads scan the same slant track in sequence and repeatedly. However, the sign
Heretofore, several proposals to eliminate the error resulting from the above have been proposed. For example, the angle of inclination of the total slant track cylinder may be changed so that the video heads follow the recorded tracks 2 and 3, even when the tape is idle. This is suggested in U.S. Pat. No. 3,375,331. French Pat. No. 2,107,066 suggests the vertical adjustment of the tape feed at the slant track cylinder. IBM Technical Disclosure Bulletin, June 1969, pages 33/34 suggests reciprocal movement of the video heads axially during each rotation of the head. Unfortunately, none of the above can be employed if for tape saving purposes, the slant tracks are recorded immediately adjacent to each other without any guard band and if they are recorded with different azimuth angles in order to eliminate cross talk. For example, a known device uses two video heads for recording and reproducing, wherein the azimuth angle of the gap of the one video head is 15° in clockwise direction and the azimuth angle of the gap of the other video head is 15° in counterclockwise direction. With this embodiment it is impossible to obtain a distortion-free still picture recording by means of repeated scanning of the same track, even if one of the above mentioned means for compensating for the differing angle between the scanning direction of the heads and the inclination of the recorded track is used.
SUMMARY OF THE INVENTION
The above and other beneficial objects are attained in accordance with the present invention by providing a method for the distortion-free reproduction of slant track magnetic video tape wherein adjacent tracks, each containing a field, are recorded and scanned without any guard band therebetween by means of two video heads which rotate in a common plane with different azimuth angles. One of the video heads is displaced axially with respect to the other head by a distance equal to one slant track width of the magnetic tape.
BRIEF DESCRIPTION OF THE DRAWINGS
In the accompanying drawings:
FIG. 1 is a plan view of a length of magnetic tape having slant tracks immediately adjacent to one another recorded thereon;
FIG. 2 is a simplified schematic drawing of a mounting arrangement for video heads in accordance with the present invention;
FIG. 3 is a wind up of the ring of FIG. 2; that is, FIG. 3 sets forth the height of ring 13 as a function of angular displacement proceeding for a full 360° about the ring;
FIG. 4 is a block diagram of a circuit for carrying out the present invention electronically; and,
FIG. 5 is a waveform diagram of various outputs of the circuit of FIG. 4.
DETAILED DESCRIPTION OF THE PREFERRED EMBODIMENT
In accordance with the present invention, an arrangement is provided to compensate for the different angles o
f the slant track when the tape is idle or moving. Reference is made to FIG. 2 wherein a first embodiment of the invention is depicted schematically. Two video heads 5 and 6 which differ in their azimuth angles are mounted on the head wheel 7 on spring plates 8 and 9. The video heads 5 and 6 are adjusted by screws 10 and 11 to their desired position, that is, so that they lie in a common rotational plane for the normal operation. A ring 13 is provided in the lower stationary slant track cylinder 12. Ring 13 can be shifted from the solid line position of FIG. 2 to the position of FIG. 2 as shown in the dotted lines, when the device is switched from normal picture reproduction to still picture reproduction. The ring 13 is divided, as shown in FIG. 3, so that its upper edge rises linearly through half its circumference. The amount of change, which is denoted by the letter "X" is equal to the width of a slant track on the magnetic tape. Plungers 14 and 15 engage the upper edges of ring 13. The distance "X" corresponds to an axial displacement of one track width taking into consideration the lever transmission on springs 8 and 9. Plunger 15 is shorter by the distance X than plunger 14. As a result, the video head 5 is displaced with respect to video head 6 by a complete track width when the ring 13 is displaced into the position indicated by the dotted lines. When rotating the head wheel 7 both video heads move axially in accordance with the upper edge of ring 13 and thereby follow the recorded tracks 2 and 3 of FIG. 1.
A circuit for carrying out the inventive method with purely electronic means is shown in FIG. 4. In this embodiment the axial adjustment of the one video head by one track width
and the subsequent axial guiding of both video heads in accordance with the recorded tracks is carried out in a commonly known manner wherein the video heads are mounted on electromechanical transducers, for example, piezoceramic elements. The control voltages for the piezoceramic must be obtained from the scanned video signals. Accordingly, the tracks must be provided with suitable signals which, on the one hand should not interfere with the chrominance signals, and on the other hand must be readable for a video head with the "wrong" azimuth angle. For these reasons only very low frequencies are used for the signal frequencies. The frequencies should be beneath the chrominance subcarrier.
In accordance with this embodiment of the invention, synchronizing pulses of the video signal are applied to the terminal 16 (see FIG. 4) and are separated in separator 17 and fed to a filter 18 which supplies constant line pulses. A voltage controlled oscillator 19 oscillates at a median frequency of, for example, 16 times line frequency, and synchronizes the line pulse received from filter 18 across the dividers 20, 21 and 22 through phase comparator 23. A further divider 24 is coupled to the inverting output of 20. The inverted and noninverted outputs of 21 and 24 are fed to a multiplexer 25 which multiplexes the outputs by approximately 90° with respect to each other in the sequence of D1, D2, D3 and D4 as shown in FIG. 5.
Vertical blanking pulses received from separator 17 are filtered in the filter device 26 (which separates the ver
tical signal) and are converted to regular frame signals in 27. The frame signals are fed to the multiplexer 25 (input A) and are also fed to divider 28, the output of which is also fed to the multiplexer (input B).
Multiplexer 25 operates as a quadruple converter and switches the D-voltages in series in accordance with logical orders from its A and B inputs. This is shown schematically in FIG. 5. The output voltage of multiplexer 25 is filtered in filter 29 and fed to the center top of switch 30. This voltage may then be fed to a terminal 31 through switch 30 and from there the output voltage is added to the frequency modulated video signal before recordation. Since each halfwave of voltage A corresponds to a field and thereby to a slant track, a voltage of quadruple line frequency is superimposed to the frequency modulated video signal and the phase of the superimposed signal changes from slant track to slant track by about 90°. Simultaneously, the divided frame pulses in 28 are fed to a pulse shaper 32 wherein they are converted as shown in FIG. 5 in such a manner that when they are added to the video signal across terminal 33, one or a plurality of follow up equalizing pulses in the vertical signal of the first field of every second frame is blanked out. In this manner each slant track is coded by virtue of the phase of the D-voltage which superimposes the frequency modulated video signal and the start of each second frame by gating the follow up equalizing pulses. The frequency of the code signals is lower than the frequency ranges for chrominance and brightness and is locked to the line frequency.
0 commenti:
Post a Comment
The most important thing to remember about the Comment rules is this: The determination of whether any comment is in compliance is at the sole discretion of this blog’s owner. Fair people are getting fair reply. Spam and useless crap and shitty comments / scrapers / observations goes all directly to My Private HELL without even appearing in public !!!
Requiring blog comments to obey well-defined rules does not infringe on the free speech of commenters.
Resisting the tide of post-modernity may be difficult, but I will attempt it anyway.
Your choice.........Live or DIE.
That indeed is where your liberty lies.
Note: Only a member of this blog may post a comment.